Unlocking Efficiency: The Role of Brewery Production Software
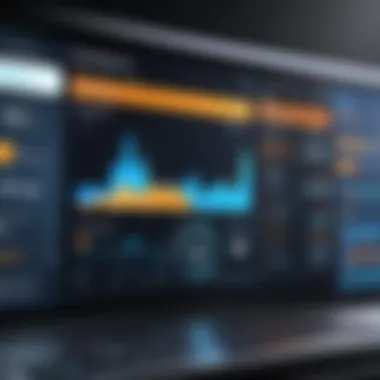
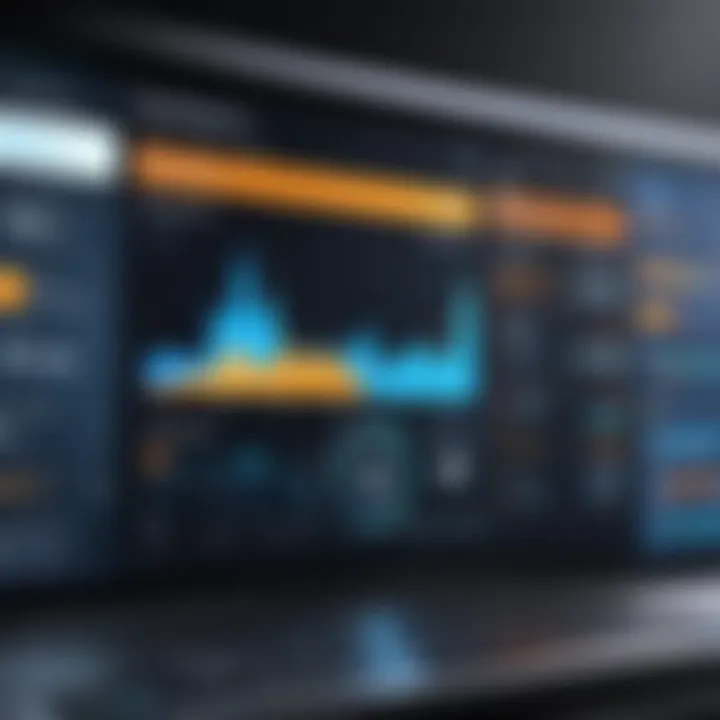
Intro
Brewery production software represents a significant advancement in the brewing industry's operational processes. As breweries grow in scale and complexity, the need for effective management tools becomes paramount. This software provides crucial functionalities that help streamline production, manage inventory, and ensure compliance with industry regulations. By understanding these tools, brewery owners and IT managers can make informed decisions to optimize production efficiency, which ultimately leads to better profitability.
Software Overview
Software Description
Brewery production software encompasses a variety of solutions designed specifically for the brewing industry. It integrates various processes involved in beer production, from tracking ingredient sourcing to managing batch production and sales. This software often includes modules that address unique challenges faced by breweries, such as seasonal fluctuations in demand and the need for quick response times to market changes. By centralizing information and automating processes, these systems help breweries operate more efficiently.
Key Features
When selecting brewery production software, it is essential to evaluate several key features:
- Production Management: This enables breweries to plan, track, and optimize production schedules, ensuring timely delivery of products.
- Inventory Control: Effective inventory management maintains balanced stock levels of raw materials and finished products, preventing shortages or overstock situations.
- Compliance Tracking: Given the strict regulations in the brewing industry, software that assists with compliance and reporting can help avoid costly penalties.
- Real-Time Reporting: Access to real-time data allows for prompt decision-making and adjustments in production processes.
- Mobile Compatibility: Mobile access enables brewers to monitor operations remotely, providing flexibility and responsiveness to operational needs.
"Utilizing brewery production software not only simplifies operations but also positions breweries for scalable growth in a competitive market."
Pricing Models
Understanding pricing models is crucial when evaluating brewery production software. Typically, two primary models are offered:
Subscription Options
Many software providers offer subscription-based models, which usually include:
- Monthly or annual fees
- Regular updates and maintenance
- Access to customer support
- Cloud-based solutions that reduce infrastructure costs
One-Time Purchase
For some businesses, a one-time purchase option is appealing. This model typically includes:
- A lump-sum payment for permanent software access
- Potential additional fees for updates and support
- Greater control over software hosting and data security
Prelims to Brewery Production Software
Brewery production software has a pivotal role in the modern brewing industry. As competition rises and consumer demands shift, breweries must adapt swiftly to remain relevant and efficient. The right software can help breweries streamline operations, manage costs, and improve product quality. This section will explore the foundational aspects of brewery production software, laying the groundwork for the discussions in subsequent sections.
Definition and Overview
Brewery production software refers to specialized tools designed for managing the diverse aspects of brewery operations. These applications include functionalities for production management, inventory control, and quality assurance. Such software enables brewery owners and staff to track various processes from fermentation to packaging. The essence of this software lies in its ability to integrate numerous functions into one platform, improving visibility and control over production workflows. Moreover, the system often provides analytics features, such as performance metrics and trend analyses, which can be critical in informed decision-making.
Historical Context
The origins of brewery production software can be traced back to the early days of industrial brewing, when manual processes dominated. As breweries grew larger and production complexity increased, the need for better operational management became evident. Initially, spreadsheet applications served as a stopgap measure. However, these tools lacked the agility required for growing breweries. In response, dedicated software solutions emerged, encapsulating industry-specific needs such as compliance with health regulations and managing raw material sourcing. Thus, brewery production software has evolved into a necessity for modern brewing operations, essential not only for efficiency but also for sustainability in a challenging market.
Key Features of Brewery Production Software
Brewery production software presents key elements that influence operational efficiency. A thorough understanding of these features helps in making informed decisions when selecting the right tool. Each element plays a vital role in streamlining operations and maximizing productivity.
Production Management
Production management is a critical component of brewery production software. This feature focuses on overseeing the entire brewing process from start to finish. It allows users to plan and schedule production runs efficiently. By tracking each batch, breweries can ensure consistent quality and minimize waste.
With production management tools, breweries can:
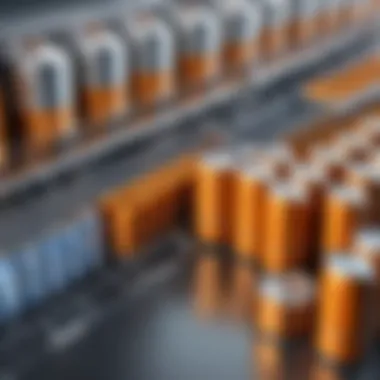
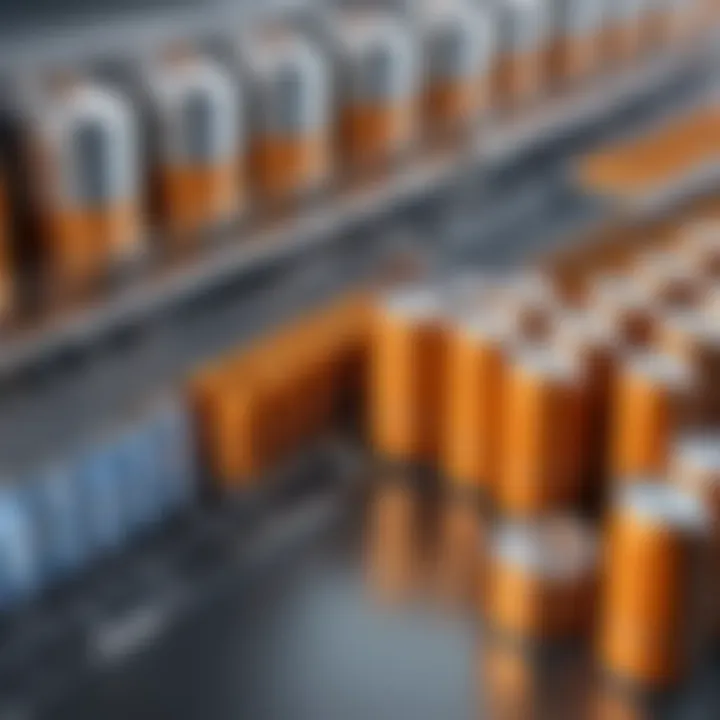
- Develop detailed recipes for various beers, ensuring each batch aligns with predefined specifications.
- Monitor fermentation and conditioning processes in real-time to identify any potential issues.
- Utilize historical data for better forecasting and planning.
This capability greatly enhances the operational aspect of breweries, making sure that timelines are met and resources are allocated effectively.
Inventory Control
Effective inventory control is essential for breweries to manage raw materials and finished products. Proper inventory management prevents shortages and overstocking, which can lead to financial losses or wastage. Brewery production software offers tools that allow for:
- Real-time tracking of ingredients and beer stock levels.
- Automatic reordering of supplies when stock reaches a specific threshold.
- Visibility of inventory across multiple locations if applicable.
This ensures that every stage of the brewing process is equipped with the necessary resources without hindering production.
Quality Control Tracking
Quality control tracking is vital in maintaining the integrity and reputation of a brewery. Using software for this purpose allows breweries to systematically address and monitor quality standards throughout the brewing process. Key aspects include:
- Logging quality metrics for each batch.
- Conducting sensory evaluations and chemical analyses.
- Generating reports that highlight deviations from quality norms.
This feature helps in not only meeting regulatory standards but reinforces customer trust by consistently delivering high-quality products.
Sales and Distribution Management
Sales and distribution management is another significant feature of brewery production software. It empowers breweries to manage their sales activities from order processing to delivery efficiently. This module includes:
- Tracking orders from customers and ensuring timely fulfillment.
- Managing relationships with distributors and retailers.
- Monitoring sales performance through analytics to identify trends.
With these insights, breweries can adjust their marketing strategies or product offerings to better meet consumer demands and improve overall profitability.
Benefits of Implementing Brewery Production Software
Brewery production software offers various advantages that can significantly enhance a brewery's operations. In today's competitive landscape, adopting such software can change how breweries manage their resources, track production, and ensure quality. The benefits discussed here are crucial for breweries aiming to optimize their production processes. The importance of implementing brewery production software is emphasized by the following elements:
Efficiency and Productivity Gains
Efficiency is a primary reason why breweries invest in production software. Automation of repetitive tasks reduces human error and saves time. For example, breweries can schedule production runs and monitor progress in real-time. This capability allows brewers to respond quickly to potential issues, thus minimizing downtime. Production software often integrates with existing systems, creating a cohesive environment that enhances workflow.
Moreover, with features like automated inventory tracking and reporting, breweries can manage their resources better. This helps in reducing waste and optimizing usage of raw materials. Such efficiency leads to higher productivity levels, allowing breweries to produce more while using fewer resources.
Enhanced Decision-Making Capabilities
Decision-making in breweries can be improved through data-driven insights provided by production software. Real-time metrics give managers crucial information about production rates, quality control, and inventory levels. This enables informed choices about production scheduling, resource allocation, and market demand.
The ability to analyze trends over time allows brewery owners to plan for growth. They can identify successful products or processes and replicate them. Additionally, having a clear overview of operational data aids in forecasting future needs, which is essential for strategic planning.
Cost Reduction and Profitability
Implementing brewery production software can lead to notable cost reductions. When operations run efficiently, the cost of labor and materials is lowered. Automation reduces the need for excess staffing, enabling breweries to allocate human resources more effectively.
Furthermore, with accurate inventory management, breweries can avoid overproduction and wastage. Cost savings ultimately enhance profitability. A streamlined production process allows breweries to focus on quality, potentially increasing sales as customers seek out their products. The improved financial health can pave the way for expansion or new investments.
Regulatory Compliance Assistance
The brewing industry faces various regulations regarding quality, safety, and environmental impact. Brewery production software can assist in maintaining compliance with these laws. Advanced tracking capabilities ensure that all processes meet established standards. Software can also generate reports required by regulatory bodies, simplifying documentation efforts and reducing the burden on brewery staff.
Compliance not only protects the brewery from potential legal issues but also builds consumer trust. Transparency about production practices can resonate with customers, enhancing brand loyalty. As the industry continues to evolve, utilizing software that supports compliance will be an essential aspect of successful brewery operations.
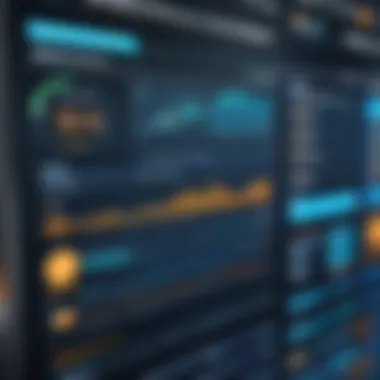
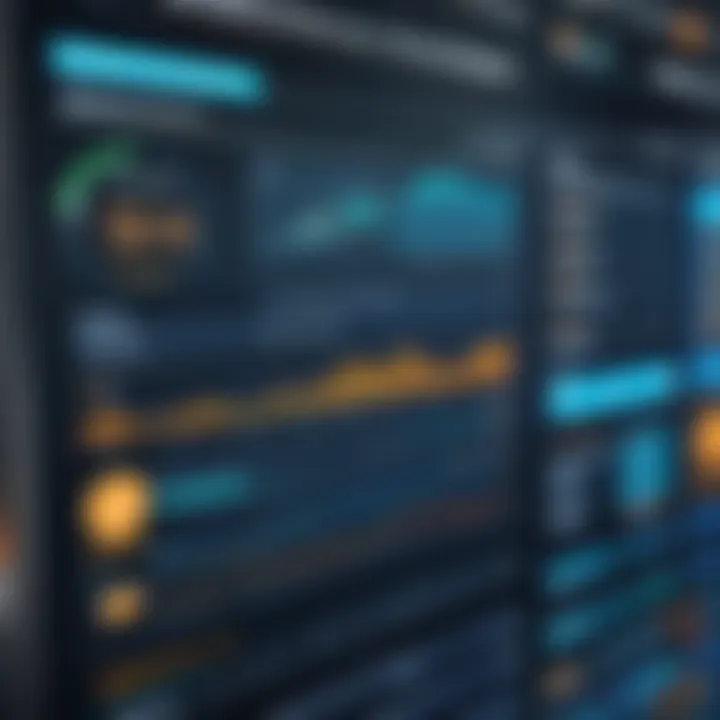
"Investing in brewery production software is investing in the future of your brewery" - Industry Expert
Challenges in Brewery Production Software Adoption
The adoption of brewery production software can be crucial for enhancing operational efficiency. However, various challenges may hinder this process. Recognizing these obstacles is necessary for a successful implementation. This section covers the primary challenges that breweries face when adopting production software.
Resistance to Change
One of the most significant hurdles is resistance to change among staff and management. Many employees are accustomed to existing workflows and may feel threatened by new technology. This resistance stems from a fear of the unknown and concerns over job security. If the staff does not embrace the change, software implementation may fail, leading to wasted resources. Brewery owners should prioritize change management by communicating the software's benefits. Training sessions can help improve staff confidence in using new tools.
Integration Issues with Existing Systems
Another challenge lies in integrating new software with existing systems. Breweries often rely on legacy systems that may not easily connect with modern software solutions. For example, a brewery may use an outdated inventory control system, making it difficult to synchronize data with the new production software. This can lead to data silos, where information is trapped in separate systems. Proper planning and collaboration with software vendors can mitigate these issues. Understanding the compatibility of new software with existing infrastructure is essential in choosing a solution.
Cost of Implementation
The cost of implementing brewery production software can be a significant barrier. Not only is there the upfront cost of software purchase, but also ongoing expenses related to training, maintenance, and support. Smaller breweries may struggle to justify these expenditures, particularly if they have limited budgets. It is important for breweries to assess the long-term return on investment when considering software options. A careful analysis can reveal whether the benefits in efficiency and productivity outweigh the initial costs. This financial perspective can help in making informed decisions about adopting new technology.
"Understanding and addressing these challenges is vital for successful adoption."
Choosing the Right Brewery Production Software
Selecting the appropriate brewery production software is crucial for optimizing operations and increasing efficiency. It is not merely about finding a tool; it is about finding the right fit that aligns with the unique needs and goals of a brewery. This section will delve into critical elements to consider when making this choice, outlining the assessment of business needs, criteria for software comparison, and the vendor selection process.
Assessment of Business Needs
Before jumping into software selection, a brewery must first assess its business needs. This entails identifying the specific requirements that the software must fulfill. An analysis should focus on various operational aspects, such as production volume, inventory management, and quality control practices.
It is recommended to engage with different teams within the organization—production, sales, and finance—to gather diverse perspectives on what features will enhance efficiency. For instance:
- Production: Do you need robust tracking for brewing processes?
- Sales: Is there a need for better sales forecasting tools?
- Finance: What financial metrics will guide your decision-making?
This collaborative approach will paint a clearer picture, ensuring that the selected software enhances all facets of the operation. Additionally, understanding the growth trajectory of the brewery is vital. Future scalability should be at the forefront of any discussion about software capabilities.
Software Comparison Criteria
After assessing business needs, the next step involves establishing criteria for comparing software options. This process can often become overwhelming due to the variety of solutions available in the market.
Key criteria to evaluate include:
- User-Friendliness: How easy is it for staff to navigate the software?
- Customization: Can the software be tailored to fit specific brewing processes?
- Integration Capabilities: How well does it work with existing systems, such as accounting or inventory management?
- Support and Training: What level of customer support is offered? Are training resources available?
- Cost: Does the software provide a clear return on investment?
Creating a weighted scoring system can help objectively compare different software products based on these criteria.
Vendor Selection Process
The final step in choosing the right brewery production software involves the vendor selection process. This stage is crucial as it defines the partnership the brewery will engage in with the software provider.
Important factors to consider during this phase include:
- Reputation: Look into reviews and case studies to gauge the vendor’s reliability.
- Experience in Brewery Sector: Has the vendor worked with similar businesses? Industry-specific experience can be a significant advantage.
- Demo and Trial Period: Can you test the software before committing? A demo or trial allows you to evaluate its functionality in real-world scenarios.
- Contract Terms: Assess the terms of service, including support and upgrade details.
"A thoughtful vendor selection process mitigates risks and ensures the chosen solution aligns with operational goals."
In sum, focusing on these components will aid in making an informed decision when selecting brewery production software. This strategic choice has lasting implications on the operations, profitability, and scalability of a brewery.
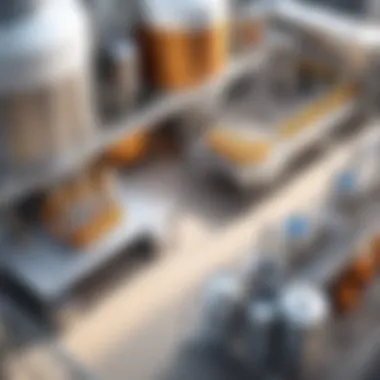
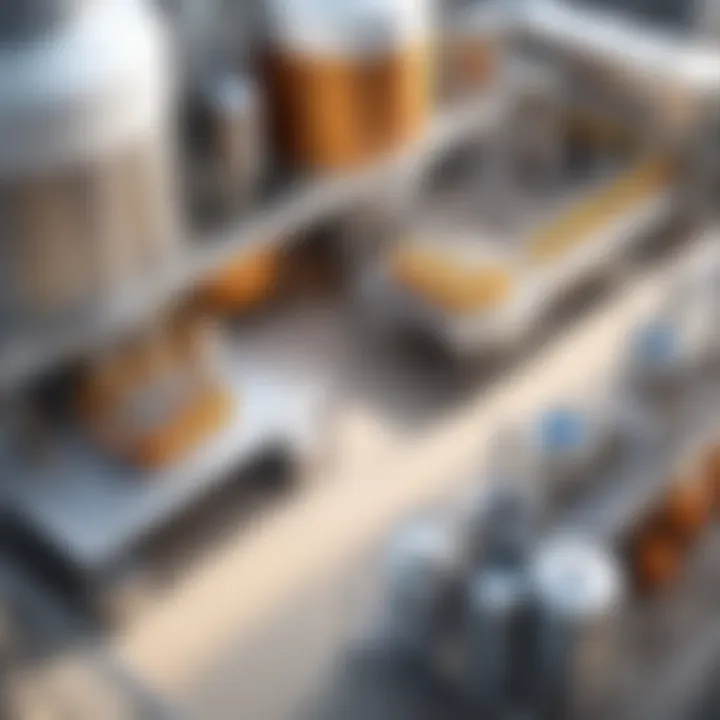
Case Studies of Successful Implementations
Case studies provide valuable insights into how real-world breweries have successfully adopted production software. These examples highlight the specific challenges faced, the decision-making process involved, and the resulting benefits. By closely examining these instances, readers can grasp not just theoretical knowledge but practical applications of brewery production software.
Successful implementations serve several essential purposes. They illustrate the process of adapting technology to meet unique brewery needs. Moreover, they demonstrate measurable outcomes that can encourage other breweries to adopt similar solutions. A well-documented case study allows potential users to compare their situations against those of established businesses, revealing what could work for them.
Large Brewery Case Study
In the case of Sierra Nevada Brewing Co., a well-known large brewery in California, the transition to sophisticated brewery production software was aimed at scaling operations while maintaining quality. This brewery faced challenges related to managing a rapidly growing output.
The software they chose was designed to handle production management, inventory control, and quality assurance. The integration of these capabilities allowed Sierra Nevada to streamline processes across different departments. Workers reported significant improvements in cross-department communication and data accessibility. They could more readily monitor supply chain dynamics and inventory levels.
The investment paid off. They achieved a 30% reduction in production errors and a 20% decrease in operational costs over two years. Customer satisfaction also saw an uptick, as products met market demand effectively. These results underline the critical role that tailored software solutions can play in large-scale operations.
Microbrewery Case Study
A contrasting yet equally compelling example is provided by Ardent Craft Ales, a microbrewery based in Virginia. With a focus on crafting innovative beers, Ardent recognized early on the importance of an agile production system. Their brewery used a simpler but very effective production software focused on batch tracking and inventory management.
Initially, the brewery struggled with manual tracking, leading to inconsistencies and waste in production. After implementing the new software, Ardent streamlined their workflow significantly. The change allowed for real-time monitoring of batch performance, which helped in adjusting recipes more dynamically.
The software also improved customer engagement by integrating a point-of-sale system to track sales trends live. This delivered actionable insights that guided Ardent in their product offerings. Sales increased by 50% within the first six months, proving that even smaller operations can achieve impressive gains with the right tools.
"Innovative software solutions can transform both large and small breweries’ operations while simultaneously enhancing product quality and customer engagement."
In summary, both case studies highlight the impact of brewery production software. These examples advocate for a careful selection process and implementation strategy tailored to the operational scale of the brewery, ensuring that technology truly serves its purpose.
Future Trends in Brewery Production Software
The brewing industry continuously adapts to new technologies and evolving consumer preferences. Future trends in brewery production software are vital for staying competitive. These trends focus on enhancing efficiency, reducing waste, and increasing profitability.
Artificial Intelligence and Automation
Artificial Intelligence (AI) plays a crucial role in brewery production software. AI enhances forecasting accuracy in production schedules, allowing breweries to manage resources better. Automated systems streamline tasks such as inventory management and quality control. These systems can analyze data from past production runs, enabling predictive maintenance. This reduces downtime and prolongs equipment life. Moreover, automation minimizes human error, ensuring consistent product quality.
"AI not only boosts efficiency but also empowers breweries to innovate their product offerings."
Businesses are encouraged to invest in AI-driven analytics platforms. These platforms help in decision-making by providing real-time data insights. As breweries scale, AI applications become increasingly necessary to handle larger volumes of data.
Sustainability and Eco-Friendly Practices
Sustainability is a growing consideration in brewery production software. As environmental responsibility becomes a priority, many breweries seek software that supports eco-friendly practices. This includes tracking energy usage, waste management, and water consumption. Analytics can help identify areas for reducing waste and optimizing resource use, thus promoting sustainable brewing methods.
By integrating sustainability metrics into their operations, breweries can comply with regulations and improve their brand image. Consumer demand for eco-conscious products drives this trend, making it essential for breweries to adopt greener practices.
Mobile and Cloud Solutions
Mobile and cloud-based solutions offer significant advantages for brewery production software. Cloud computing enables breweries to access critical data from anywhere. This provides operational flexibility and real-time collaboration among team members. With mobile applications, staff can monitor production processes and update inventory on-the-go.
These solutions enhance transparency and facilitate communication within teams. They can also provide customers with up-to-date information about product availability. Additionally, cloud solutions often come with lower upfront costs and easier scalability options, making them an attractive choice for breweries of all sizes.
Finale
In the realm of brewery production, the choices made concerning software can have deep implications on operational efficiency, quality control, and profitability. This article has explored the multifaceted nature of brewery production software, underscoring its role as an essential tool for navigating the complexities of modern brewing practices. As breweries grow in scale and sophistication, the need for tailored software solutions only increases.
Summary of Key Points
The features of brewery production software such as production management, inventory control, and compliance tracking are not just add-ons but are vital components that influence day-to-day operations. The benefits of using such software include increased efficiency, enhanced decision-making, improved regulatory compliance, and cost reduction. However, adopting these systems is not without challenges, such as resistance to change and integration issues with existing systems. The article has also highlighted key features to consider when selecting software, which can aid decision-makers in aligning software capabilities with business needs.
Final Thoughts on Brewery Production Software
Brewery production software stands at the intersection of tradition and innovation within the brewing industry. It is essential for breweries, regardless of size, to assess their unique requirements and choose software solutions that provide tangible benefits. As technology continues to evolve, embracing these advanced tools will not only improve operational workflows but also enhance the overall quality of the brewing process. For brewery owners and IT managers looking to optimize production, leveraging the right software will be a key factor in long-term success.