Goods Order Inventory Management: Strategies for Success
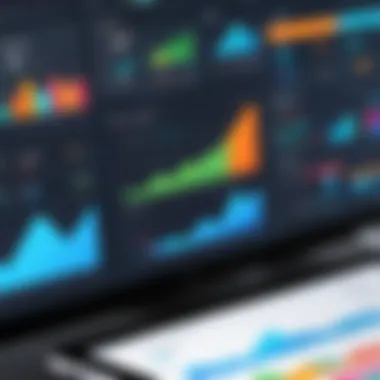
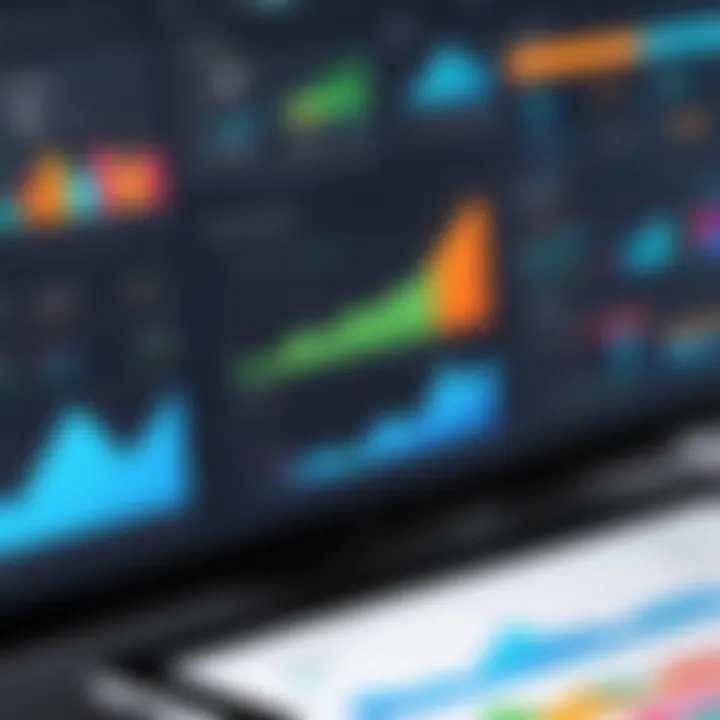
Intro
Inventory management isn't just about keeping track of what's on the shelf anymore. For modern businesses, it’s akin to brain surgery— a delicate operation requiring precision and skill. With customer expectations soaring ever higher and market trends shifting like sand, mastering goods order inventory management can be the difference between thriving and simply surviving.
So why is effective inventory management essential? In the world of real-time data and rapid order fulfillment, businesses must optimize stock levels to not only meet demand but also minimize excess costs associated with overstocking. This article aims to delve into essential strategies and tools that should be part of any savvy business's toolkit. Whether it's through leveraging data analytics or integrating new technologies, the road to operational excellence is paved with smart inventory management choices.
Importance of Inventory Management
The significance of inventory management can’t be overstated. Poor management can lead to stockouts that result in lost sales, or worse, unhappy customers. On the flip side, maintaining high stock levels ties up capital that could be better deployed elsewhere. Companies must navigate these challenges thoughtfully, staying ahead with methods that sharpen their operations.
"An efficient inventory process is not just a safety net for your business; it's its backbone."
This article will unravel various strategies to enhance your inventory framework, tailored specifically for decision-makers in organizations keen on optimizing their operational models. Time to roll up those sleeves and dive into these impactful tactics.
Understanding Goods Order Inventory
In the ever-evolving landscape of business, grasping the nuances of goods order inventory isn't merely beneficial; it’s fundamental. The ability to manage inventory efficiently can mean the difference between victory and defeat in the competitive arena. Initially, one might think of inventory as just a collection of stock, but in reality, it embodies much more. It reflects a company's operational pulse, balancing supply and demand meticulously, with every misstep leading potentially to disastrous consequences, be it lost sales or excess holding costs.
Moreover, understanding goods order inventory encompasses strategies that lay the groundwork for operational success. For example, a sound inventory management approach can enhance customer satisfaction by ensuring that the right products are available at the right time. This is invaluable, as missed opportunities due to stockouts can tarnish a brand’s reputation. On the flip side, overstocking ties up precious capital and can lead to wastage if products become obsolete or perish. Thus, a well-thought-out inventory system facilitates optimal stock levels that not only cut costs but also enhance customer loyalty and retention.
To sum up, understanding goods order inventory is crucial for both micro and macro operations in a business structure. It’s not simply about counting widgets; it’s about weaving together a holistic picture that ensures efficiency and effectiveness throughout the supply chain.
Definition of Goods Order Inventory
Goods order inventory refers to the stock of goods that a business procures with the intention of reselling. This inventory is pivotal for business operations, encapsulating products in various stages of availability—from raw materials awaiting transformation to finished goods ready for sale on the shelves. Essentially, it represents what a company has on hand to meet customer demand.
An important aspect of this definition is that goods order inventory is not a static element. It encompasses dynamic processes that relate to purchasing, storage, and sales. Tracking these movements effectively allows companies to maintain an adequate stock level while minimizing the costs associated with excess inventory.
Importance in Supply Chain Management
The significance of goods order inventory in supply chain management can’t be overstated. Think of it as the linchpin of the entire operation. Properly managed inventory leads to smoother production cycles and delivery schedules, directly impacting operational efficiency. It helps in anticipating demand trends, thus facilitating better decision-making.
- A few key benefits of efficient goods order inventory management include:
- Cost Reduction: Efficient inventory management can significantly reduce storage costs by ensuring that surplus stock is minimized.
- Accuracy in Forecasting: Having reliable inventory data can enhance demand forecasting accuracy, allowing businesses to anticipate customer needs more effectively.
- Improved Supplier Relationships: When inventory levels are accurately tracked, businesses can communicate regularly with suppliers, ensuring timely replenishment and avoiding stockouts.
The Role of Inventory Management Systems
In the realm of goods order inventory management, the effectiveness of operations hinges significantly on the role of inventory management systems. These systems serve as the backbone for ensuring that the whirlwind of ordering, stocking, and delivering goods is executed with precision and efficiency. It's not just about keeping count of what’s on hand; it's about fostering a dynamic environment where data and decision-making go hand in hand. The strategic use of these systems can yield numerous benefits that directly affect an organization’s bottom line.
One major reason inventory management systems are pivotal is their ability to provide real-time visibility into stock levels. Imagine being able to know the exact quantity of each item in your inventory across all locations at any given moment. This transparency leads to better decision-making and drastically reduces the risk of overstocking or understocking — two chronic issues many businesses face.
Moreover, an efficient inventory system streamlines the procurement process. When suppliers can be connected directly to the inventory data, reorder triggers can automate supply restocking. This not only saves time but also leads to more accurate ordering, further minimizing excess inventory costs.
Thus, understanding the role these systems play isn’t merely academic; it’s a matter of operational survival in a competitive marketplace. Unforeseen fluctuations in supply or demand can derail a business if not handled adeptly. That's where these systems come into play, acting as a safety net that scales with business needs.
"An efficient inventory management system is like a well-oiled machine, keeping the organization running seamlessly through the chaos of supply and demand."
Overview of Inventory Management Systems
An inventory management system refers to the technology that helps businesses track and manage inventory levels, orders, sales, and deliveries. These systems can range from simple tools — such as spreadsheets — to advanced software solutions that leverage algorithms and artificial intelligence. A sophisticated inventory system helps businesses handle the complexities that arise when dealing with thousands of products and multiple locations. With features that facilitate tracking, forecasting, and reporting, an effective system can provide a comprehensive view of inventory, helping businesses adjust to fluctuations in market demand.
Key Features to Consider
When choosing an inventory management system, several key features must be evaluated:
- Real-time Inventory Tracking: This feature enables businesses to monitor stock levels continuously, ensuring that they can respond swiftly to changes in demand.
- Order Management Capabilities: It should streamline the ordering processes, allowing for easier task management and seamless integration with e-commerce platforms.
- Forecasting Tools: Advanced systems often include predictive analytics, enabling businesses to anticipate inventory needs based on historical data.
- Reporting Functions: Comprehensive reporting and analytics can help identify trends and patterns, informing future inventory strategies.
- Integration Options: The ability to integrate with existing tools (like accounting or CRM systems) is vital for smooth operations.
Comparison of Popular Systems
In today's market, numerous inventory management systems vie for attention. A few of the popular options include:
- NetSuite: Known for its robust ERP capabilities, it offers comprehensive inventory tracking and integration features. Ideal for medium to large enterprises.
- TradeGecko: This cloud-based solution excels in e-commerce integrations and is tailored for small to medium-sized businesses.
- Zoho Inventory: Offers a free tier, making it accessible for startups and smaller operations while being feature-rich enough for scaling businesses.
- Fishbowl: A system that boasts strong manufacturing and warehouse management tools, perfect for businesses that operate on a larger scale.
- Square for Retail: If integrated payment processing fits your needs, this is an excellent choice, especially for retailers looking for simplicity.
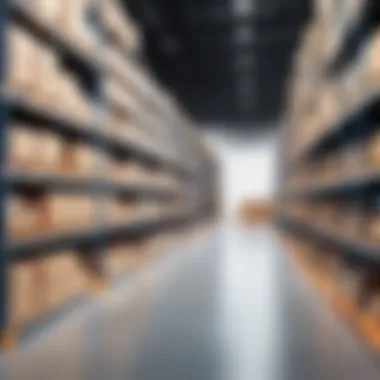
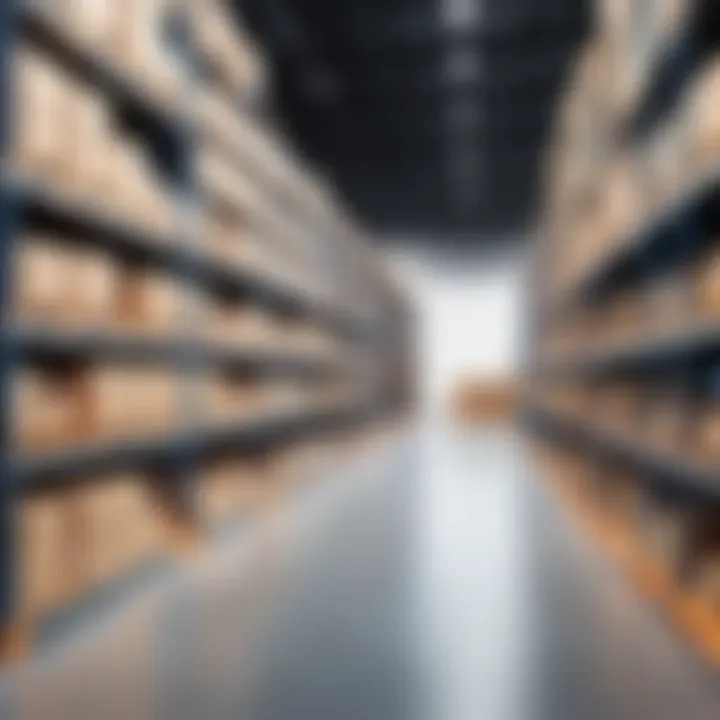
Each system offers unique benefits and potential downsides depending on the specific needs of a business. Selecting the right one requires careful consideration of both current requirements and future growth.
Techniques for Effective Goods Order Management
Managing goods effectively is like juggling; each technique demands precise timing and skill to keep everything in motion without dropping the ball. Successful businesses know that efficient inventory management isn't just about maintaining stock; it's about optimizing the whole process. Techniques such as Just-In-Time (JIT), Economic Order Quantity (EOQ), and ABC Analysis offer practical frameworks that organizations can adapt for their unique needs, ultimately leading to better customer satisfaction and reduced operational costs.
Just-In-Time (JIT) Inventory
Just-In-Time inventory is like a well-timed clock. The philosophy behind JIT is all about reducing waste by receiving goods only as they are needed in the production process. This approach minimizes inventory costs and keeps cash flow healthy.
Why is JIT valuable? It allows businesses to reduce storage expenses and minimize the risk of overstocking, which can tie up capital in unsold goods. For instance, consider a car manufacturer that applies JIT: they only order parts just before they need them on the assembly line. This approach not only saves space but also facilitates quicker responses to market demands.
"JIT inventory reduces lead times and can make a business incredibly agile, a necessity in today’s fast-paced market."
However, this strategy is not without its challenges. Businesses must have reliable suppliers and efficient logistics. Any hiccup in the supply chain can halt production, so thorough vetting and communication with suppliers is critical.
Economic Order Quantity (EOQ)
Economic Order Quantity, often abbreviated as EOQ, serves as a crucial formula for determining the optimal order quantity that minimizes total inventory costs, which includes holding costs, order costs, and stockout costs. Understanding EOQ is paramount for businesses that aim to strike a fine balance between surplus and scarcity in their inventory.
The EOQ formula involves several factors including demand rate, ordering costs, and holding costs. Essentially, it provides a systematic way to figure out how much to order and when. For example, a coffee shop might calculate the EOQ of its beans to maintain consistent supply without over-purchasing. Using EOQ leads to reduced wastage and saves money, allowing businesses to allocate resources more effectively.
ABC Analysis
Lastly, ABC Analysis categorizes inventory into three classes based on importance. This strategy helps decision-makers prioritize their efforts where it counts the most.
- A items: These are very important to the company's success and typically a small percentage of total items but account for a large portion of inventory value.
- B items: These are of moderate importance, often treated with regular management practices.
- C items: These are the least valuable and represent the bulk of items in terms of volume but contribute minimally to overall value.
For instance, a retailer might stock hundreds of items, yet only a few generate significant revenue. By focusing on A items, the retailer can streamline efforts and resources where they will have the most impact. Using this analysis not only plays a vital role in inventory optimization but also aids in making informed purchasing decisions.
Challenges in Goods Order Inventory Management
In the modern landscape of supply chain management, confronting the various challenges of goods order inventory management can't be overstated. These hurdles aren't simply obstacles; they hold the potential to significantly influence the operational flow, financial health, and competitive edge of businesses. Recognizing, understanding, and devising solutions to these challenges is crucial for firms aiming for seamless operations and optimized inventory levels.
Inventory Shrinkage
When discussing inventory management, inventory shrinkage emerges as a notable concern. This term encompasses the loss of inventory that can occur through various means, including theft, damage, or miscounting. It’s like a sneaky thief in the night that impacts profit margins without a sound. For businesses, shrinkage creates an immediate financial strain. Basic calculations reveal that if a company has a shrinkage rate of merely 2%, it can dramatically cut into its bottom line, especially when operating on thin margins.
Taking proactive measures can help mitigate this issue. For instance, implementing security technology, conducting regular audits, and training staff in loss prevention strategies can help tackle shrinkage effectively. A company’s culture can also play a pivotal role; fostering an atmosphere of trust and diligence often leads to decreased shrinkage rates, as employees feel more accountable and engaged.
Overstock and Understock Issues
Equally problematic are the issues of overstocking and understocking. Over time, businesses might find themselves in a cycle of fluctuating inventory levels, leading to these twin challenges. Overstocking often results in unnecessary storage costs, wastage, and cash flow issues. It's akin to filling a bathtub without a drain; water will overflow, costing you more to manage. Conversely, understocking can lead to missed sales opportunities, frustrated customers, and a tarnished reputation. Imagine wanting a product, only to be told it's out of stock.
Strategy is essential when combating these issues. Minimizing stock discrepancies can involve embracing forecasting techniques that utilize historical data and market trends. Additionally, employing just-in-time inventory methods can help align stock levels closely with actual demand, decreasing the risks associated with both overstock and understock scenarios. Not to forget, technology can aid here too, with sophisticated inventory management systems that track product movements and trends, providing relevant insights to guide decisions.
Supplier Reliability and Lead Time Variability
Another challenge businesses face is supplier reliability and the variabilities in lead time. The dependency on suppliers can be a double-edged sword. When they fulfill orders reliably and on time, operations run smoothly. However, disruptions in the supply chain can lead to production delays, unexpected costs, and unfulfilled customer demand. This unpredictability can feel like navigating a minefield.
To address these anxieties, companies must cultivate relationships with multiple suppliers to reduce reliance on a single source. Contract negotiations should include clear expectations regarding lead times and penalties for delays. Furthermore, creating contingency plans can be beneficial. By ensuring that alternatives are available, the risks of variabilities can be minimized, and the business can maintain a consistent flow of goods, safeguarding customer satisfaction and brand loyalty.
"Investing in quality suppliers and maintaining open lines of communication can transform the supply chain from a vulnerability into a strength."
In summary, the obstacles faced in goods order inventory management vary but are critical to address. Identifying problems such as inventory shrinkage, overstocking/understocking, and supplier inconsistencies not only helps in strategic planning but also in achieving operational efficiency and enhancing overall business performance.
Utilizing Technology for Inventory Optimization
In today’s fast-paced business environment, optimizing your goods order inventory through technology is not just an option; it’s a necessity. As companies grapple with the challenges of inventory management, the integration of technology emerges as a linchpin for enhancing efficiency and minimizing costs. By leveraging technological solutions, businesses can better manage stock levels and provide just-in-time delivery, which is increasingly vital in a market where customer expectations are at an all-time high.
The transformative impact of technology ranges from streamlining processes to providing real-time insights. Organizations gain the ability to make informed decisions based on accurate data, which can significantly enhance operational frameworks. The following examines the key components of this technological integration, focusing on data analytics, automation tools, and the role of artificial intelligence.
The Role of Data Analytics
Data analytics has emerged as a game-changer in inventory management, allowing firms to make sense of vast amounts of information. It’s not simply about collecting data; it's about converting that data into actionable insights. By analyzing sales patterns, customer behavior, and forecast trends, businesses can predict demand more accurately.
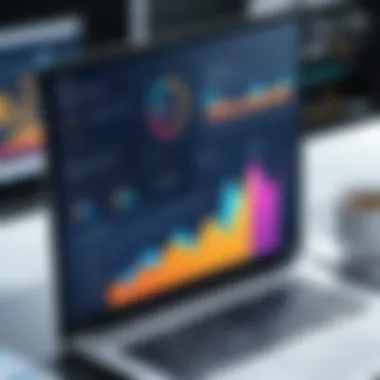
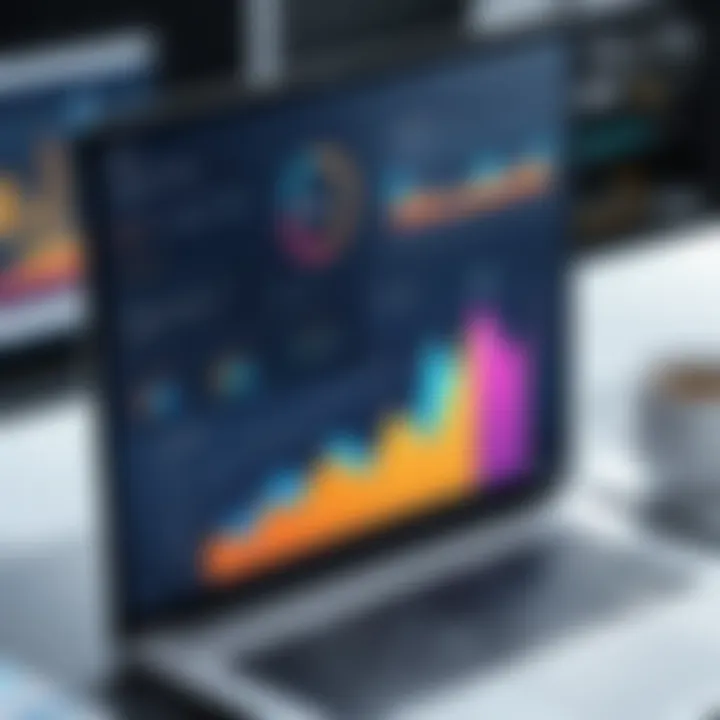
With precise demand forecasting, a company can avoid the pitfalls of overstocking or understocking. For instance, using tools like Google Analytics can shape your inventory strategy based on real-time customer interactions. This means more informed decisions regarding which items to order and in what quantities. Ultimately, smarter inventory replenishment methods can lead to reduced holding costs and enhanced customer satisfaction.
"Utilizing advanced analytics enables businesses to thrive in complexity, turning potential chaos into well-coordinated action."
Automation Tools in Inventory Management
Inventory management systems are no longer just databases; many have evolved to incorporate automation tools that enhance efficiency at every level. These tools can automatically track inventory levels, order supplies when they dip below optimal thresholds, and even signal when it's time for audits or reviews. For small to medium-sized businesses, this can mean a significant reduction in manual labor, allowing employees to focus on value-added activities rather than tedious inventory counts.
Some popular automation tools include:
- Fishbowl: Provides advanced inventory management, facilitating stock tracing and order processing.
- Zoho Inventory: Offers sales and purchase tracking capabilities, along with integration options for e-commerce.
- TradeGecko: Known for its user-friendly interface, enabling seamless inventory control across multiple channels.
Employing these automation strategies can result in faster response times to changing demands, enhancing the whole supply chain's resilience.
Integrating Artificial Intelligence
Artificial Intelligence (AI) is revolutionizing inventory management by introducing next-level decision-making capabilities. By automating routine tasks and analyzing complex variables, AI helps in recognizing patterns that might be missed with traditional methods. This capability enhances the forecasting processes further, allowing businesses to interpret and act upon data in real-time.
AI-driven tools can also optimize reordering processes based on predictive analytics. For example, a company could use AI algorithms to analyze both external factors like market trends, seasonal variations, and even internal factors such as historical sales data to determine the best times to restock certain products. The outcome? Better management of inventory levels and less wastage.
To implement AI effectively, consider platforms like Llamasoft or IBM Watson, which offer advanced analytics and machine learning capabilities tailored for supply chain and inventory management.
In summary, leveraging technology in inventory management provides significant benefits, transforming operations into a more fluid and responsive process. Organizations that prioritize these technological integrations will not only improve efficiency but also pave the way towards a more sustainable and profitable future.
Implementing Best Practices
Implementing best practices in goods order inventory management is a cornerstone of ensuring operational efficiency. When organizations embrace these practices, they not only enhance their inventory processes but also foster an adaptive culture that can respond quickly to market changes. Best practices act as a roadmap, guiding businesses through the often turbulent waters of inventory challenges. It primes the enterprise for smooth sailing by reducing waste, enhancing accuracy, and optimizing stock levels.
Regular Inventory Audits
Regular inventory audits serve an important role in keeping a finger on the pulse of inventory health. These audits are crucial, as they provide insights into stock levels, identify discrepancies, and help pinpoint issues before they snowball. Imagine trying to navigate through fog without visibility; that's what managing inventory without audits feels like. Typically, organizations choose between two types of audits: periodic and perpetual.
- Periodic Audits: These are conducted at set intervals, usually monthly or quarterly. They give a snapshot of operations but can overlook immediate concerns.
- Perpetual Audits: This is a continuous process, allowing businesses to monitor stock levels in real-time.
By incorporating regular audits, companies can achieve a clearer understanding of their inventory status. This can help to catch any issues related to inventory shrinkage or overstocking and ensure compliance with financial standards. Remember, it’s not just about checking boxes; a thorough audit can reveal trends—like what products are flying off the shelves versus those gathering dust.
Vendor Managed Inventory ()
Vendor Managed Inventory (VMI) takes the traditional supplier-buyer relationship and flips it on its head. Here, vendors take charge of managing their products in the buyer's inventory. This model can bring a multitude of benefits, from minimizing stockouts to lowering holding costs. With VMI, the vendor becomes responsible for monitoring inventory levels and replenishing stock according to predefined criteria.
Consider how this shifts the burden of making timely inventory decisions away from the buyer. This system can foster stronger partnerships across the supply chain, as both parties work closely towards common objectives. Key considerations in utilizing VMI include:
- Trust: Building a high level of trust between the vendor and the buyer.
- Clear Communication: Maintaining seamless communication regarding stock levels and transfer processes.
- Data Sharing: Providing vendors access to the necessary data for effective inventory management.
In this approach, risks are shared, and the potential for cost savings can be significant.
Employee Training and Engagement
No strategy would succeed without the right people backing it up. Employee training and engagement take center stage when it comes to implementing best practices in inventory management. Fully engaged employees not only contribute to a harmonious work environment, they also help in executing the inventory strategies effectively.
Training isn’t just about familiarizing workers with software or systems; it’s about building a solid foundation of understanding regarding inventory principles. This can be done through:
- Regular Workshops: These can cover various aspects of inventory management or new technologies being implemented.
- Encouraging Feedback: Employees on the ground often have valuable insights; their input should be actively sought out.
- Cross-Training: By involving employees in various roles related to inventory, organizations make it easier for teams to adapt during crunch time.
Engaged and well-informed employees take ownership of their tasks, which can lead to better outcomes in terms of efficiency and accuracy.
"The path to effective inventory management lies not just in the systems but in aligning human resources towards a common goal."
Implementing best practices in goods order inventory management creates a robust framework, ensuring that organizations remain lean and agile in their operations.
Future Trends in Inventory Management
In the dynamic landscape of supply chain management, staying ahead of the curve is fundamental for businesses aiming to enhance their operational efficiency. Future trends in inventory management not only emphasize efficiency but also integrate pivotal elements of sustainability and technology. As firms navigate through uncertainties in global markets, these trends herald both challenges and opportunities that decision-makers must take into serious consideration.
Sustainability in Inventory Practices
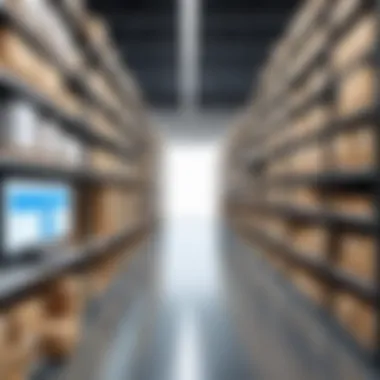
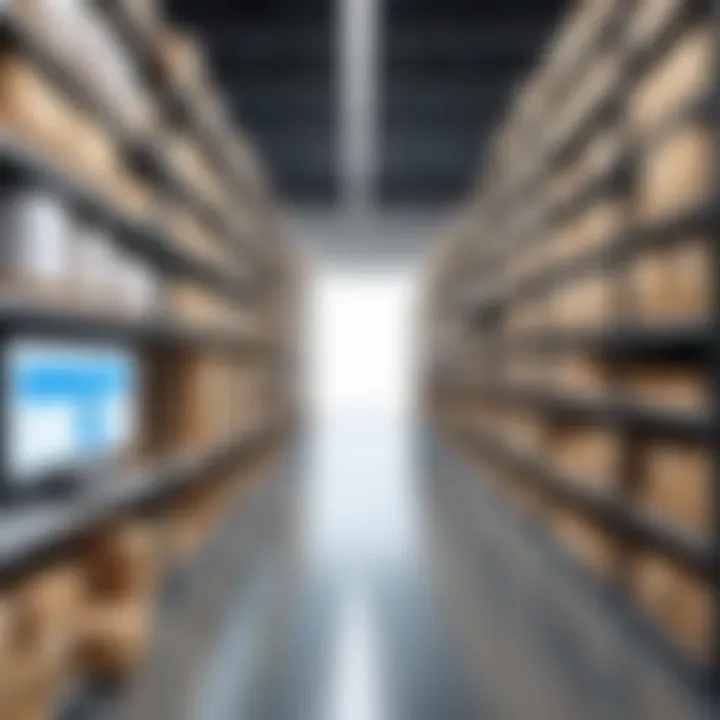
In today’s age, sustainability isn’t just a buzzword; it’s becoming a critical element of inventory management. Adopting eco-friendly practices can greatly impact the long-term viability of a business. Companies are increasingly recognizing the necessity to reduce waste and optimize resources. This leads to several approaches:
- Use of Sustainable Materials: Companies are now sourcing biodegradable or recycled materials for their packaging, reducing their carbon footprint.
- Energy-Efficient Warehousing: Upgrading existing warehouses with solar panels or energy-efficient lighting systems results in cost reductions and lower environmental impact.
- Circular Economy Models: These models enable businesses to design for longevity and recyclability. In practical terms, this could mean embracing product life-cycle assessments and resale strategies to minimize resource consumption.
By prioritizing sustainability in inventory practices, organizations not only attract environmentally-conscious consumers but also create a brand image that resonates with modern market values.
The Impact of E-commerce
The surge of e-commerce has radically transformed inventory management strategies. With a growing number of consumers preferring online shopping, businesses need to adapt swiftly. Key impacts include:
- Real-Time Inventory Tracking: Online retailers need to ensure that stock levels reflect reality. If a customer orders a product that has already been sold, this leads to dissatisfaction.
- Flexible Inventory Models: Businesses must balance inventory between centralized warehouses and local fulfillment centers to meet customer demands efficiently. This is especially crucial during peak shopping seasons.
- Data-Driven Decision Making: E-commerce platforms provide a wealth of data. This information can dictate inventory reorder levels, predict trends, and optimize stock based on consumer behavior.
These shifts require a strategic overhaul of traditional inventory management systems, making adaptability more essential than ever.
Blockchain Technology in Inventory Management
Blockchain isn’t just for cryptocurrency anymore. It’s emerging as a transformative tool in the realm of inventory management. The key benefits include:
- Enhanced Transparency: Each transaction recorded on the blockchain is immutable and verifiable, allowing for greater supply chain transparency. Stakeholders can track every item from the supplier to the end consumer, reducing chances of fraud.
- Improved Traceability: In industries like food and pharmaceuticals, being able to trace the exact source and journey of a product can protect consumers and enforce compliance with regulations.
- Streamlined Orders and Payments: By facilitating smart contracts, blockchain can automate order placements and streamline payments, significantly reducing lead times.
"Implementing blockchain technology could very well be the key to attaining a seamless inventory management experience, ensuring trust among all supply chain participants."
The changes brought by these innovations hint at a future where inventory management is not just about handling goods but also about strategic thinking and agility. As businesses embrace these future trends, they stand poised to not only survive but thrive in an increasingly complex market.
Case Studies: Success Stories in Inventory Optimization
Examining real-world case studies offers profound insights into effective goods order inventory management strategies. This section underscores how leading organizations have navigated the treacherous waters of inventory challenges, harnessing innovative approaches to optimize their supply chains. The emphasis here lies not merely in theoretical discussions but in tangible benefits that stem from these success stories.
These cases illuminate several aspects:
- Practical Applications: Showcasing successful strategies that can be replicated across various industries.
- Lessons Learned: Identifying mistakes others made to avoid falling into the same traps.
- Innovation: Highlighting the creative solutions deployed that transformed their inventory operations.
- Quantifiable Benefits: Providing metrics that demonstrate the effectiveness of implemented strategies, like reduced costs or improved turnaround times.
"It’s not just about managing inventory; it’s about managing your business’s potential through smarter inventory choices."
Leading Retailers and Their Strategies
Retail titans like Walmart and Amazon have set the bar high when it comes to inventory management. Their innovative strategies provide numerous lessons for others in the field.
- Walmart: This giant employs a robust data analytics system that tracks inventory in real-time across its vast network of stores. They use a method called cross-docking, which allows products to move rapidly from suppliers to shelves, reducing storage time and costs. This strategy not only minimizes overstock issues but also ensures that customers find what they want when they need it.
- Amazon: Known for its agility, Amazon has developed its proprietary fulfillment centers where automation plays a pivotal role. Their use of AI and machine learning predicts which items will be needed at specific times and locations, enhancing both efficiency and customer satisfaction. By deploying dynamic pricing and stock adjustments, they can react swiftly to market demands, making their inventory management highly adaptive.
Manufacturers Adapting to Changes
The landscape for manufacturers is shifting, with many adapting to changes uniquely. Companies such as Tesla and Toyota illustrate how staying ahead means embracing flexibility and innovation.
- Tesla: This electric vehicle manufacturer focuses on vertical integration, controlling the supply chain to an unprecedented degree. They leverage technology to keep tight reins on their inventory levels, adopting a just-in-time model. This approach not only streamlines their production but also mitigates risks related to excess inventory, especially during market fluctuations.
- Toyota: Renowned for its Toyota Production System, the company utilizes continuous improvement and a pull system. By synchronizing production schedules with actual demand, Toyota efficiently reduces waste while ensuring high production rates. Their ability to pivot and adapt to customer needs and supply chain disruptions showcases their commitment to efficient inventory management.
These case studies collectively demonstrate that effective inventory management strategies are not one-size-fits-all but rather tailored solutions that consider specific organizational contexts and market conditions. Learning from these successful examples can empower other businesses to implement their own effective inventory management strategies.
The End and Key Takeaways
In the realm of goods order inventory management, wrapping up the discussion necessitates a firm grasp on both the theoretical and practical aspects developed throughout the article. The sung emphasis here is on effective strategies and practices which not only help in optimizing inventory but also in fostering a robust supply chain. As dynamic market landscapes shift alongside technological advancements, businesses must adapt their approaches to inventory management in significant ways.
A vital consideration that emerges from the preceding sections is the undeniable role of data analytics and technology. These components usher in a new era of precision and foresight, allowing decision-makers to navigate uncertainties with greater confidence. You see, by leveraging comprehensive data, organizations can predict trends more effectively, identify potential pitfalls, and respond proactively. This leads to improved stock levels and fewer disruptions.
Summary of Effective Strategies
Here’s a concise recap of some effective strategies:
- Just-In-Time (JIT) Inventory: This approach cuts down excess inventory costs by aligning orders closely with production schedules.
- Economic Order Quantity (EOQ): It balances ordering costs with holding costs to determine the optimal order size. This helps minimize total inventory costs over time.
- ABC Analysis: This method categorizes inventory into three groups, allowing businesses to focus on controlling the most critical items.
- Automation Tools: Utilizing software solutions can significantly enhance efficiency in tracking, ordering, and auditing stock. Technologies like RFID and barcoding simplify processes, helping to mitigate human error.
- Regular Inventory Audits: Scheduled reviews ensure that inventory records align with physical stocks, making discrepancies easier to spot.
- Vendor Managed Inventory (VMI): This practice allows suppliers to manage inventory levels, reducing stockouts and ensuring timely replenishment.
Final Thoughts on Inventory Management Practices
After dissecting inventory management practices, it stands out clearly that an agile approach is necessary. Acknowledge that this field is ever-evolving, and the means of achieving optimization shift as new tools and methodologies emerge. The integration of Artificial Intelligence and data analytics isn’t just a trend; it has become essential for those wishing to remain competitive.
Moreover, the commitment of the whole organization towards continuous improvement and employee training can transform not just the inventory process, but the entire operational framework of a business. As companies look ahead, adopting a mindset of flexibility while embedding strategic practices will undoubtedly foster long-term success.
Key takeaway: To sustain profitability and efficiency, businesses must embrace innovative strategies in goods order inventory management and stay vigilant about industry trends.
Given the fierce competition and customer expectations in today's market, the practices outlined here provide a solid groundwork for any business aiming to enhance their inventory management approach. As the saying goes, "A stitch in time saves nine," and in inventory management, this could not ring truer.
Making these practices habitual can pave the way for not just survival, but thriving in your industry.