Streamline Your Business with QuickBooks Inventory Tools
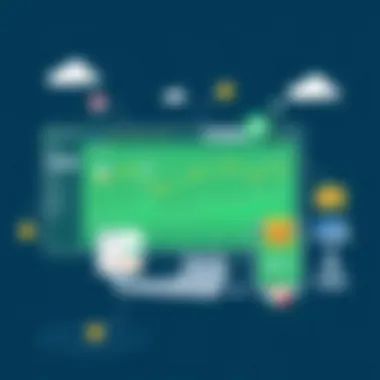
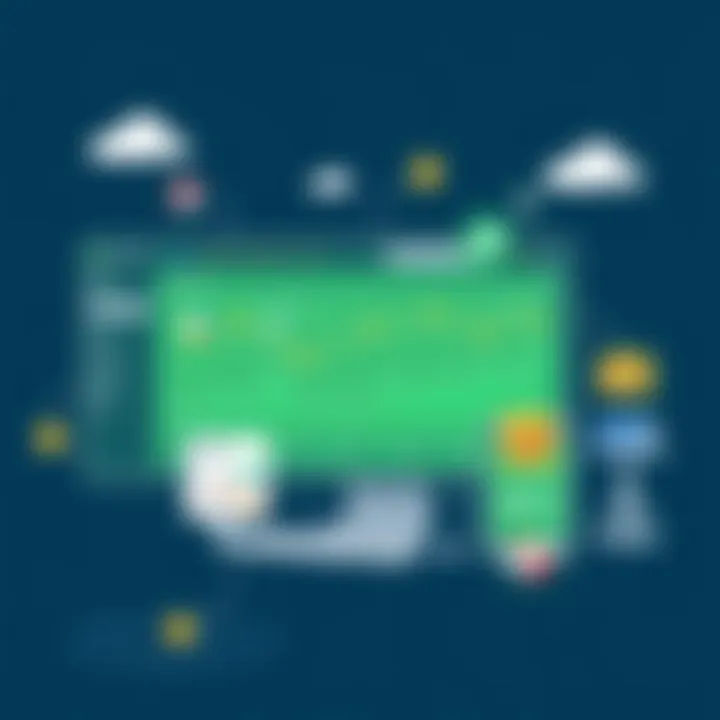
Intro
In the dynamic world of manufacturing, having an edge in managing inventory can mean the difference between success and stagnation. QuickBooks Manufacturing Inventory Management Software emerges as a pivotal tool designed specifically to cater to the intricate needs of manufacturing businesses. This software not only elevates operational efficiency but also aligns with the complexities that come with tracking materials, products, and resources within the manufacturing ecosystem.
As businesses grapple with the challenges of inventory management, such as demand forecasting, stock tracking, and supply chain integration, tools like QuickBooks offer a structured approach. It's not just about keeping tabs on what’s in stock; it’s about orchestrating a symphony of operations, ensuring that every component works harmoniously toward production goals.
In rambling through the features, benefits, pricing options, and challenges faced while employing this software, we commence our exploration of QuickBooks’ distinctive capabilities tailored for manufacturing firms. By demystifying these elements, decision-makers can gain clear visibility into whether QuickBooks is the right fit to bolster their inventory management processes.
Preface to QuickBooks Manufacturing Inventory Management Software
Understanding how inventory is managed is critical, especially in the manufacturing sector. This introduction sets the stage for a deep dive into the functionalities offered by QuickBooks Manufacturing Inventory Management Software. The focus here is to illuminate how this software can be a game-changer for manufacturers, addressing specific challenges like tracking parts, managing raw materials, and optimizing resources to ultimately enhance production efficiency.
Inventory management in manufacturing goes beyond just keeping track of goods. It's about making sure that every component flows seamlessly from the supplier to the production line, while also keeping an eye on costs and timeliness. QuickBooks, known for its user-friendly interface and robust capabilities, enters the arena as a vital tool for businesses aiming to streamline inventory processes. This will enable manufacturers to gain a firmer grip on their supply chain.
Defining Inventory Management in Manufacturing
Inventory management can be defined as a series of practices aimed at overseeing and controlling the ordering, storage, and use of components that a company needs to complete its operations. In manufacturing, this includes not just finished goods but also raw materials, work-in-progress items, and components. It’s akin to keeping the pieces of a jigsaw puzzle in order to construct the bigger picture of business success.
Accurate inventory management involves more than glancing at stock levels. Manufacturers must maintain an accurate count of items on hand and in transit. This often requires using sophisticated systems to track various attributes of inventory such as quantity, location, and status.
Mismanagement can lead to substantial financial losses. Consider a manufacturer who finds itself overstocked with components that are suddenly out of demand; the money spent on that inventory could have been better allocated. Therefore, adopting a skillful inventory management system is not a luxury but a necessity.
The Role of QuickBooks in Inventory Management
QuickBooks plays a crucial role in the inventory management landscape for manufacturers. This software does not just simplify tracking but also automates several processes that traditionally consumed valuable time and resources. With QuickBooks, manufacturers can gain insights into inventory costs, sales trends, and supplier performance.
- Real-time tracking is perhaps one of the standout features. Manufacturers can see which items are selling and which are gathering dust.
- Automated alerts notify users when stock levels are low or over the target limits. This allows responding to inventory needs swiftly.
- Integrating QuickBooks with other systems enhances visibility across the supply chain, ensuring that every part of the process is accounted for.
Key Features of QuickBooks Manufacturing Inventory Management Software
In the intricate realm of manufacturing, possessing a robust inventory management system is critical for maintaining a seamless operation. QuickBooks Manufacturing Inventory Management Software stands out by offering a suite of features tailored to meet the unique challenges faced by businesses in this sector. By focusing on key functionalities, this software significantly contributes to better control over inventory processes, operational efficiency, and resource utilization. Let's delve deeper into the essential features that QuickBooks brings to the table.
Real-Time Inventory Tracking
One prominent feature of QuickBooks is the real-time inventory tracking capability. This functionality ensures that business owners have up-to-the-minute information about stock levels. It helps in avoiding overstock and stockouts, situations that can be detrimental to a company’s reputation and financial health. When a order is placed, any materials used are automatically deducted from the inventory count. This synchronicity prevents unforeseen shortages and streamlines the manufacturing process.
"Real-time inventory tracking transforms chaotic stock management into a well-oiled machine, enabling swift decision-making based on accurate data."
The ease of access to current inventory data empowers managers to identify trends, make informed predictions, and respond promptly to market demands. Moreover, with mobile access, staff can check stock levels while on-the-go, making sure they stay updated no matter where they are.
Automated Reordering Systems
Next up is automated reordering systems. QuickBooks not only gives users an overview of existing stock but also triggers restocking orders based on preset thresholds. This eliminates the guesswork and ensures that materials are ordered well before they run out. By maintaining optimal stock levels, businesses can enhance their cash flow and avoid delays in production caused by insufficient resources.
Implementing this feature is like having a trusted assistant who never forgets to reorder supply. The consistency it brings to operational cadence cannot be overstated, particularly in a fast-paced production environment.
Costing and Pricing Tools
Having a handle on costs is imperative for any manufacturing business. QuickBooks includes sophisticated costing and pricing tools that help businesses track the expenses associated with materials and labor. This functionality allows for the calculation of accurate product costs, hence supporting more strategic pricing decisions. By understanding production costs better, companies can adjust prices, explore profitability, and ultimately, become more competitive in the market.
In addition, features like job costing means companies can assess performance of specific projects, enabling continuous cost optimization. Missing out on small expenses can add up in a short time, and this tool helps cut those unnecessary costs.
Integration with Supply Chain Management
Lastly, the ability to integrate with supply chain management platforms is invaluable. QuickBooks allows seamless communication between inventory management and various supply chain components including purchasing, logistics, and distribution. This interplay ensures that all arms of the business are linked, promoting harmony and efficiency.
Integration aids in data sharing and real-time updates across platforms, enhancing visibility over the entire supply chain process. It signifies that when a change occurs in inventory, all related departments can instantly adjust their strategies without lag or miscommunication. It’s the glue that holds operations together.
In summary, the features embedded in QuickBooks Manufacturing Inventory Management Software not only support routine tasks but also enhance the overall agility of manufacturing processes. By leveraging real-time tracking, automation, detailed costing, and seamless integration, businesses can navigate complexities effectively and drive toward sustainable growth.
Benefits of Implementing QuickBooks in Manufacturing
When the rubber meets the road in manufacturing, efficient inventory management can make all the difference. QuickBooks Manufacturing Inventory Management Software fits into this picture like a glove. The benefits of adopting such software are far-reaching and touch on several core areas that define operational success. Let’s explore some of the major advantages, focusing on how this software can elevate the way businesses manage their manufacturing processes.
Enhanced Operational Efficiency
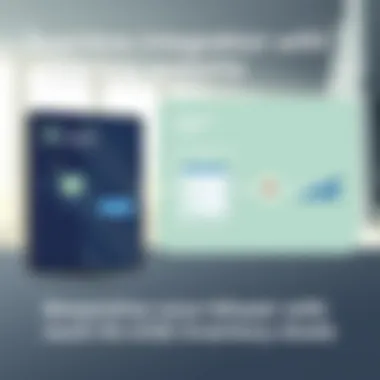
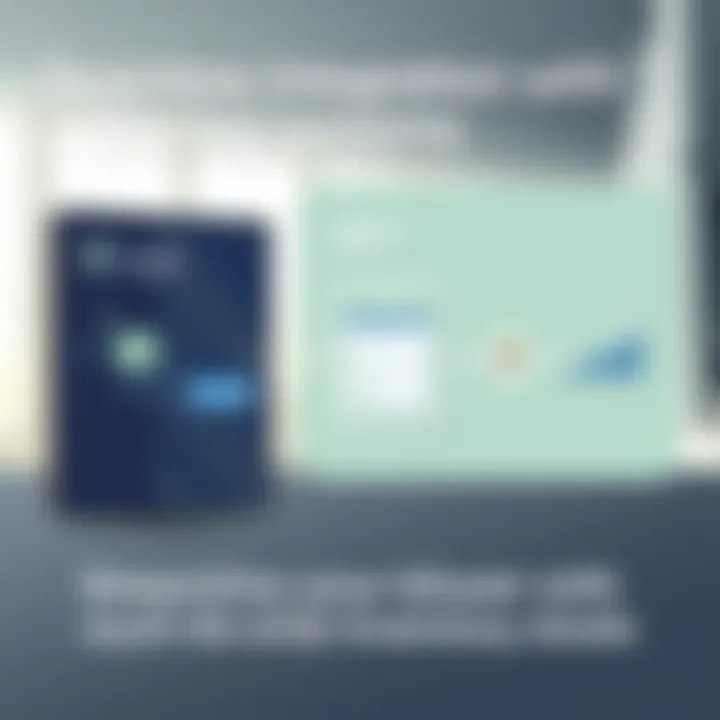
A well-oiled machine is crucial in manufacturing, and QuickBooks offers tools designed to streamline operations. By centralizing inventory, it eliminates the chaos of juggling multiple systems or spreadsheets. Instead, with a click, stakeholders can access vital data, leading to prompt decision-making.
Key aspects include:
- Streamlined workflows that remove redundancies.
- Consistent updates on inventory status help prevent delays in production.
- Automated tasks reduce manual labor, freeing up employees to focus on more strategic initiatives.
This blend of automation and real-time data access cultivates a smoother operation, allowing businesses to pivot more swiftly in response to dynamic market demands.
Improved Inventory Accuracy
In manufacturing, accuracy is not just about numbers; it’s about trust. When product counts are off, the ripple effects can lead to production delays or dissatisfied customers. QuickBooks addresses this by providing real-time tracking that sharpens inventory precision.
Consider the following benefits of accurate inventory management:
- Reduction in stockouts and overstock: By maintaining precise records, manufacturers can ensure they are not sitting on excess inventory or, worse, running out of essential parts.
- Better forecasting: Accurate data allows for improved demand forecasting, enabling companies to anticipate market changes and adjust their strategies accordingly.
- Minimized discrepancies: Regular inventory audits become less painful and more effective, cutting down on time and resources spent troubleshooting errors.
In short, enhanced accuracy translates directly into operational reliability and can carve out a significant competitive edge.
Cost Savings through Better Resource Management
Cost-cutting is often the name of the game in manufacturing, and implementing QuickBooks can pave the way for significant savings. By refining resource management practices, companies can maximize both their labor and material investments.
Here’s how:
- Reduced carrying costs: Efficient inventory management helps minimize storage costs by keeping only what’s needed. This means less capital tied up in unsold inventory.
- Efficient use of manpower: Automating certain processes reduces the need for additional staff and overtime, resulting in labor savings.
- Minimized wastage: QuickBooks enables manufacturers to track expiration dates or shelf lives, thus reducing waste associated with perishable goods or materials.
Ultimately, effective resource management supported by QuickBooks doesn’t just put money back in the pocket; it also sharpens the overall competitive position of the business.
By leveraging such software, companies not only optimize their inventory but also position themselves better to respond to market fluctuations and customer needs.
Implementation Strategy for QuickBooks Manufacturing Software
Implementing QuickBooks Manufacturing Software is a significant step for any business looking to refine its inventory management. This process encompasses more than just installing software; it requires a thorough understanding of the organization's specific needs, the careful planning of integration, and a meticulous configuration of settings. By developing a well-rounded implementation strategy, businesses can vastly improve their operational efficiency and achieve accurate inventory management without a hitch.
Assessing Business Needs
Before diving into system implementation, it’s crucial to have a firm grasp on what the business truly needs. Think of it as laying the foundation for a building. If it’s shaky from the beginning, everything that follows could be problematic.
Start by analyzing the current inventory management systems in place. Speak with employees across various departments—purchasing, sales, and production—to gather insights on challenges they face. Identify manually intensive processes, recurring errors, or slowdowns, then document these pain points. The goal is to clarify specific needs such as real-time tracking, automated reordering, or custom reporting. A solid list of prioritized features tailored to the business’s unique context will guide the entire implementation process.
Planning the Integration Process
Once you've outlined your needs, the next step is planning how to integrate QuickBooks into existing business operations. Planning is like drafting a blueprint; one miscalculation can lead to costly mistakes down the line.
When mapping out the integration, consider the following:
- Timeline: Define a realistic timeline. Identify critical milestones and set achievable deadlines.
- Stakeholders: Involve key players from various departments early in the discussion. Their input will nourish a smoother transition later.
- Data Migration: Assess the data that needs to move to the new system. Determine how to clean, format, and upload it to avoid data discrepancies post-integration.
Engage with IT personnel or external consultants to ensure the plan aligns with technical requirements and capabilities.
Configuring Software Settings
Configuration is akin to tuning a musical instrument; if done right, everything plays harmoniously together. In this phase, QuickBooks must be set up to reflect the specific operational routines of the business.
Start with:
- User Permissions: Set permissions based on job roles. This ensures the right people access the right data, preventing unauthorized changes.
- Inventory Categories: Organize inventory into logical categories that suit business processes. For example, categorize by product type or production stage.
- Automation Rules: Establish protocols for triggers, such as when stock levels fall below a certain threshold to initiate reorder. This not only saves time but also mitigates risks of stockouts.
Training Staff and Users
Finally, one cannot underestimate the importance of training. Consider it the final polish to a newly crafted product. Without appropriate training, even the most brilliant systems can fall flat.
Create a structured training program that includes:
- Workshops: Organize hands-on workshops where teams can familiarize themselves with the system. This hands-on experience breeds confidence.
- Documentation: Provide clear manuals or handouts that employees can refer to. Easy access to resources can answer questions as they arise.
- Ongoing Support: Establish a support system or a help desk for ongoing assistance post-implementation. Regular check-ins can help address any lingering issues or adapt to any evolving needs.
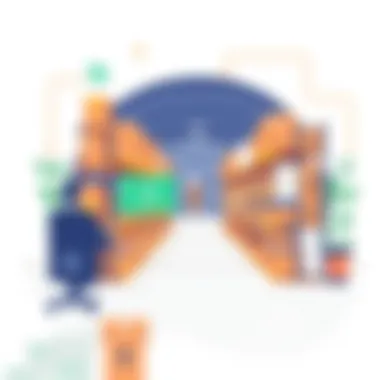
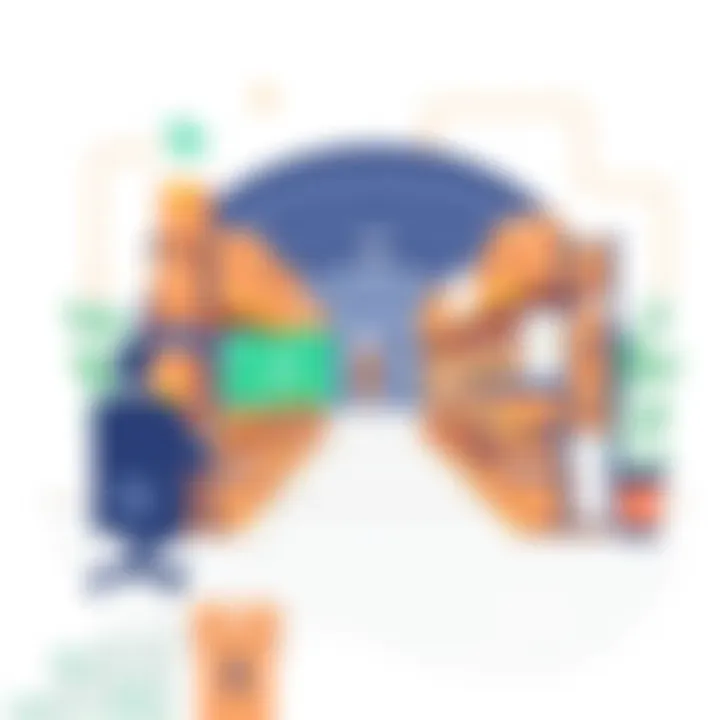
Implementing QuickBooks Manufacturing Software effectively can be the turning point for an organization striving for superior inventory management. It involves thorough assessment, careful planning, precise configuration, and robust training, all aimed at achieving optimal operational efficiency.
Addressing Common Challenges in Inventory Management
Inventory management, especially in a manufacturing context, is seldom a walk in the park. For businesses aiming to optimize their operations, it’s crucial to tackle the hurdles that can derail efficiency. Not only do these challenges affect the bottom line, but they can also result in bottlenecks that hinder productivity. Thus, highlighting the importance of addressing common challenges in inventory management becomes essential in understanding how QuickBooks Manufacturing Inventory Management Software plays a pivotal role in overcoming these issues.
Managing Excess Inventory
Excess inventory is like having your house stuffed to the brim with things you don't use—it's just wasted space. Keeping too much stock ties up capital that could be employed elsewhere and leads to increased storage costs. With QuickBooks, you can leverage real-time inventory monitoring to keep track of what’s on hand and what’s actually selling. It helps you distinguish between slow-moving items and hotcakes, making it easier to decide when to cut back.
QuickBooks facilitates alerts that notify you when stock levels surpass a certain threshold, minimizing over-purchasing. Additionally, integrating sales data can help predict demand more accurately. This means excess inventory can be reduced, freeing up resources for other essential areas of the business.
Dealing with Inventory Discrepancies
Inventory discrepancies may feel like thorny issues one can't get rid of. When stock records don't match physical inventory, that's a significant red flag. The differences often stem from human error, theft, or miscommunication among team members. It's vital to keep an eye on this, as inaccuracies can erode customer trust and lead to lost sales.
With QuickBooks, the system logs transactions meticulously. You can conduct regular reconciliations to catch discrepancies early. Moreover, it provides an audit trail that traces back to where the issue might have originated. This allows businesses to implement corrective measures quickly and makes it easier to fulfill orders accurately. Keeping clients satisfied and trust intact translates into better retention and loyalty.
Seasonal Demand Fluctuations
The ebb and flow of seasonal demand is as predictable as day turning into night, but managing its ripple effect can be tricky. Many businesses find themselves overstocked at one point and then scrambling for inventory at another. The capability to respond to these fluctuations can make or break a business.
Integrating QuickBooks with your sales data can illuminate patterns and trends in customer behavior throughout the year. By using historical data, you can forecast demand and adjust inventory levels accordingly. This proactive approach allows you to capitalize on busy seasons while ensuring idle inventory doesn’t clutter your storage facilities during off-peak times.
"Keeping a finger on the pulse of demand can mean being prepared for the waves rather than getting swept away."
In summary, the challenges of managing excess inventory, dealing with discrepancies, and responding to seasonal variations are unavoidable in the manufacturing sector. However, leveraging QuickBooks Manufacturing Inventory Management Software provides the tools necessary to address these challenges effectively. Companies can streamline their operations and improve efficiency by adopting a data-driven approach to inventory management.
Integration Capabilities of QuickBooks
In today’s fast-paced business environment, the ability to integrate various software solutions isn't just a luxury; it's become a necessity. QuickBooks stands out in the realm of manufacturing inventory management, offering robust integration capabilities that help streamline operations. The seamless communication between different systems enhances overall efficiency, minimizes data entry errors, and ultimately drives productivity. Without the right integrations, businesses might find themselves drowning in inconsistent data and inefficient processes.
Linking with E-Commerce Platforms
Connecting QuickBooks with e-commerce platforms like Shopify or WooCommerce can transform how a business operates online. This integration allows for real-time data flow between the sales channels and inventory management. Imagine a scenario where every time a product is sold online, your inventory is automatically updated in QuickBooks. This real-time tracking diminishes the risk of overselling and enhances customer satisfaction by ensuring that stock levels are accurate. It's a win-win situation; sellers spend less time on manual updates and can focus on growing their business instead.
"Efficiency is doing better what is already being done." - Peter Drucker
Additionally, these integrations open up a world of possibilities for analyzing sales trends. You can assess which products are flying off the shelves and which ones are collecting dust. Having access to this data can inform purchasing decisions, giving you a clearer picture of your inventory requirements.
Benefits of E-Commerce Integration:
- Real-time Inventory Syncing: Ensures that stock levels are up-to-date across all sales channels.
- Improved Customer Experience: Reduces instances of backorders and out-of-stocks, leading to happier customers.
- Simplified Financial Management: Automatically records sales data in QuickBooks for better bookkeeping.
- Data-Driven Decisions: Gain insights into sales trends for better planning and forecasting.
Compatibility with Other Software Solutions
Integration doesn’t stop at e-commerce. QuickBooks can also play well with various other software solutions, enhancing its functionality. Whether it's a Customer Relationship Management (CRM) tool, like Salesforce, or a warehouse management system, effective integration can lead to smoother operations. This compatibility is vital for businesses looking to create a comprehensive operational ecosystem.
By bridging the gap between QuickBooks and other software, companies can ensure that information flows freely between departments. For instance, sales teams can access inventory data while speaking with clients, ensuring they provide accurate delivery timelines. Similarly, accounting professionals can gain insights into sales and inventory trends without having to chase down numbers from different systems.
Key Advantages of Software Compatibility:
- Streamlined Workflows: Reduces delays in accessing necessary information across platforms.
- Increased Accuracy: Minimizes the chances of human error from manual data entry.
- Enhanced Reporting: Offers more comprehensive analytics by consolidating data from various sources.
- Flexibility: Allows businesses to scale by integrating new software solutions as they grow.
Being adaptable in today's technological landscape often means having software that can talk to each other. QuickBooks offers the tools for these integrations, helping businesses not only keep their fingers on the pulse of their inventory but also enable smoother processes across the board.
Evaluating the ROI of QuickBooks Manufacturing Software
Evaluating the return on investment (ROI) of QuickBooks Manufacturing Software is a crucial aspect for businesses that aim to enhance their inventory management processes. Understanding the direct and indirect returns from the investment can provide insights into whether the software implementation aligns with the strategic goals of a manufacturing business. It’s not just about the cost of purchase and implementation but also about the long-term gains in efficiency, accuracy, and profitability. Companies often overlook how much they can save through streamlined processes, reduced errors, and improved inventory oversight.
When delving into the ROI of implementing QuickBooks, several key elements come into play:
- Initial Costs: This includes the purchase price of the software, any hardware needed, and costs associated with setup and configuration.
- Operational Savings: Reduced manual labor and more efficient inventory management contribute to lower operational costs. Over time, these savings can be substantial.
- Improved Decision-Making: With accurate data readily available, businesses can make quicker and better-informed decisions, ultimately impacting profitability.
- Scalability: As businesses grow, the software’s adaptability can save costs related to transitioning to new systems or processes.
It’s essential to take a holistic view of how QuickBooks can transform not just inventory processes but the overall efficiency of the business. After evaluating these factors, one can gain a clearer picture of the potential ROI from implementing QuickBooks Manufacturing Software.
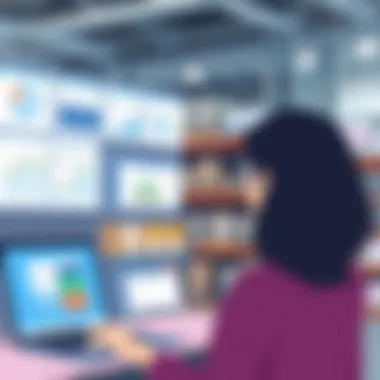
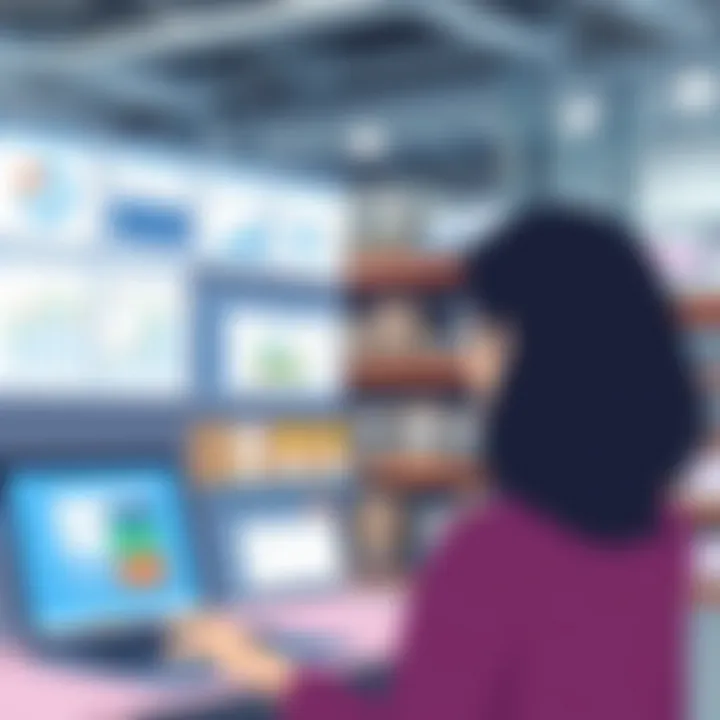
Cost-Benefit Analysis for Businesses
A solid approach to understanding the ROI of QuickBooks Manufacturing involves conducting a cost-benefit analysis. This analysis involves comparing the costs incurred by the software against the expected benefits.
- Cost Consideration:
- Benefits Consideration:
- Software purchase and licensing fees
- Ongoing subscription costs (if applicable)
- Training expenses for staff
- Possible additional costs for custom integrations
- Time saved on manual inventory counts
- Decrease in excess inventory costs
- Enhanced ability to respond to market demand changes
- Improvement in customer satisfaction through better product availability
A well-conducted analysis helps validate the financial advantages of adopting the software. For instance, if a company saves a considerable amount on labor and reduces inventory holding costs, these elements can significantly outweigh the initial costs.
Success Stories and Testimonials
Real-world applications often shed light on the tangible returns from using QuickBooks Manufacturing Software. Many businesses report significant improvements post-implementation. Taking a look at successful case studies can help illustrate this. Here are some common themes:
“Our inventory challenges were like a heavy chain; after adopting QuickBooks, we feel lighter. We’ve reduced our excess stock by 30% in just six months.”
From testimonials gathered, companies shared the following benefits:
- Efficiency Gains: Businesses often mention how they have streamlined operations and reclaimed time that was previously spent on tedious manual tasks.
- Enhanced Accuracy: Many noted the reduction in human error, which has empowered their decision-making with reliable data.
- Financial Visibility: Users appreciate real-time insights into inventory management, enabling them to anticipate needs ahead of time.
A deep-dive into these stories showcases the common thread of profitability improvement and operational excellence. They serve as a strong testament to QuickBooks’ value, helping potential users envision the benefits waiting for them.
Future Trends in Inventory Management Software
As industries evolve, so do the tools we use to manage key processes like inventory. Future trends in inventory management software are crucial not just for efficiency, but for maintaining competitive edge in a rapidly changing business landscape. As manufacturing demands rise and technology advances, businesses must adapt and adopt new solutions that address these changing needs.
First and foremost, companies are increasingly leaning towards automation. The manual processes of yesteryear are giving way to solutions that not only save time but also reduce the chances of human error. With automation, businesses can streamline operations, resulting in smoother workflows and quicker response times.
Moreover, companies focusing on data-driven decisions stand to gain significant advantages. The ability to analyze inventory levels, sales forecasts, and supply chain dynamics in real-time enables organizations to be agile and proactive, reducing unnecessary costs and enhancing profitability. Here’s where we step into two significant sub-trends feeding into this larger trend: advancements in automation and the growing role of artificial intelligence alongside predictive analytics.
Advancements in Automation
The promise of automation in inventory management is not a far-off notion anymore. It has arrived and is changing the game across sectors. For instance, automated inventory systems use barcode technologies or RFID scans to track stock levels in real-time. When a product is sold or stocked, the system updates instantaneously, so there's no question about what is available or what needs reordering. This level of visibility allows businesses to act promptly and avoid pitfalls like stock outs or excess inventory.
Businesses are also incorporating more robust, smart automation tools that connect various parts of their operations. For example, an automated replenishment system can be linked directly to sales channels. If a spike in demand occurs, the system recognizes it and adjusts orders accordingly without manual input, saving time and minimizing errors.
As these tools become more advanced, they are also becoming more accessible to businesses of all sizes.
"In today's age, if you’re not automating, you might as well be paddling upstream without a paddle."
Artificial Intelligence and Predictive Analytics
Artificial Intelligence (AI) and predictive analytics are taking inventory management further into the future. AI allows software to learn from historical data, making it possible to forecast trends with greater accuracy. For manufacturers, the ability to predict seasonal demand or foresee potential disruptions in the supply chain can make or break the bottom line.
Predictive analytics dives deep into data patterns, enabling businesses to adjust inventory levels before issues arise. For example, a manufacturer noticing a pattern of increased sales in the summer months can stock up in advance, thus avoiding the chaos that comes with last-minute orders.
Additionally, integrating AI can help in identifying counterfeit products. This is critical in maintaining brand integrity and customer trust. For instance, companies using machine learning algorithms to cross-reference product data can detect anomalies and act swiftly to mitigate risk.
In summary, the future trends in inventory management software are fundamentally altering how businesses operate. Through both advanced automation and smart analytics, companies can not only manage their inventories more effectively but also predict future challenges and opportunities. An organization that stays ahead of these trends is better positioned to thrive in the marketplace.
Ending
Evaluating QuickBooks Manufacturing Inventory Management Software is essential for businesses looking to optimize their inventory processes. This examination connects the dots between the software’s features and tangible benefits for manufacturing operations. By understanding how QuickBooks addresses critical challenges in inventory management, organizations can make informed decisions regarding its implementation.
Summarizing Key Insights
In summary, QuickBooks offers a range of functionalities that cater to the unique demands of manufacturing industries. Some key insights include:
- Real-time inventory tracking allows businesses to monitor stock levels effectively, reducing the risk of shortages or excess.
- Automated reordering systems help ensure that essential materials arrive when needed, thus avoiding production delays.
- Integration capabilities allow QuickBooks to work seamlessly with other software tools, enhancing overall operational efficiency.
These features empower manufacturers to maintain greater control over their inventory, ultimately leading to more efficient operations and improved resource allocation.
Final Thoughts on QuickBooks Implementation
Adopting QuickBooks Manufacturing Inventory Management Software is not just about switching tools; it’s about enhancing the way a business operates. For decision-makers, understanding the complexities of this software is crucial. Here are a few considerations:
- Assess current inventory practices and pinpoint areas needing improvement before implementing QuickBooks.
- Ensure all staff are trained adequately to utilize the software effectively.
- Monitor and evaluate performance post-implementation to gauge the success and impact on operational efficiency.
Overall, the integration of QuickBooks in manufacturing operations promises significant rewards, fostering not just productivity but also strategic growth. Balancing its strengths with considerations for best practices will place a business on the path toward operational excellence.