SPC Tools: Transforming Business Operations for Quality
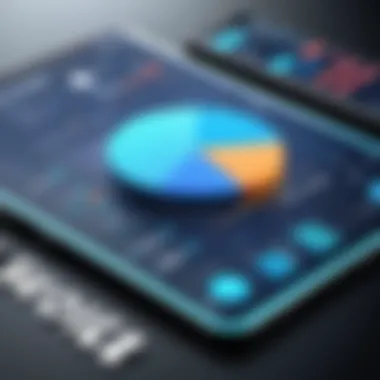

Intro
In today's competitive business environment, organizations are increasingly turning to data-driven tools to enhance their operations. One such tool is Statistical Process Control (SPC). Understanding SPC tools and their applications can greatly influence business success. This section lays the groundwork for exploring the significance of SPC in managing and improving quality within various organizational processes.
SPC focuses heavily on continuous improvement. Through the systematic use of statistical methods, businesses can identify variations and trends in their processes. By addressing these issues, companies can enhance product quality, reduce waste, and lower costs. This analysis aims to offer insights into various SPC tools, their functionalities, and the myriad benefits they provide to organizations that embrace them.
The objective is to synthesize information that helps decision-makers in business environments to understand how to effectively implement SPC methodologies. They must navigate the complexities of these tools while recognizing their potential in driving operational excellence.
Software Overview
Statistical Process Control relies on various software solutions designed to track, analyze, and improve quality processes. This section explores what these software tools entail, shedding light on how they function to meet the demands of businesses.
Software Description
SPC software encompasses a range of applications that facilitate data collection, analysis, and visualization. These tools help businesses monitor their processes over time, enabling them to identify outliers and trends. Most SPC software comes with user-friendly interfaces that allow even those with modest technical skills to engage with data effectively.
Typically, these tools integrate seamlessly with operational systems, allowing for real-time data updates. Continuous monitoring of manufacturing processes enables rapid responses to issues before they lead to quality failures.
Key Features
The effectiveness of SPC software is greatly influenced by its key features. Some core functionalities include:
- Data Visualization: Graphical representations help users quickly interpret data.
- Control Charts: Visual tools to monitor process stability and performance.
- Statistical Analysis Tools: These tools offer insights into variation reduction and process improvement.
- Real-Time Monitoring: Continuous data tracking ensures immediate action on potential issues.
- Automated Reporting: Streamlined reporting functionalities save time and reduce errors in data presentation.
Effective use of SPC tools results in significant quality improvements and operational efficiencies.
Pricing Models
Investing in SPC software requires a clear understanding of available pricing models. Organizations can choose from different purchasing strategies that align with their financial capabilities and operational needs.
Subscription Options
Many software providers offer subscription-based pricing. This model is attractive due to its lower upfront costs and the flexibility it provides. Companies can select monthly or annual plans depending on their budget and preferences. Subscription models often include regular updates, customer support, and training packages, which can enhance the adoption and success of the software.
One-Time Purchase
Alternatively, some organizations opt for a one-time purchase model. This involves paying a single fee for perpetual use of the software. While it may seem economical, it is important to consider additional costs for updates, support, and training in the long term.
Organizations must weigh the pros and cons of each model carefully. Choosing the right pricing option can be crucial for optimizing the return on investment for SPC tools.
Prologue to SPC Tools
Statistical Process Control (SPC) tools play a vital role in modern business operations. They allow organizations to monitor and control processes to ensure that they operate at their maximum potential. The importance of SPC tools can be observed in various aspects such as improving product quality, enhancing operational efficiency, and facilitating better decision-making.
These tools utilize statistical methodologies to analyze process performance. By harnessing data, businesses can identify deviations from desired performance levels. This proactive approach reduces waste and improves overall productivity.
SPC tools consist of various techniques and methods, including control charts, process capability analysis, and Pareto analysis. Each of these tools offers unique insights into process behavior. They allow teams to understand processes better and implement improvement strategies effectively.
Moreover, the significance of SPC tools extends beyond mere numbers. They foster a culture of continuous improvement within organizations. When teams engage with these tools, they become more attuned to their operations and can address potential issues before they escalate into larger problems.
In summary, the introduction of SPC tools is not just about applying statistical techniques, but about instilling a philosophy of quality and process excellence across the organization. Understanding their importance paves the way for businesses to leverage these tools to achieve sustainable growth and efficiency.
"The value of SPC tools lies in their ability to transform data into actionable insights, enabling a proactive approach to process management."
Understanding Statistical Process Control
The understanding of Statistical Process Control (SPC) is foundational for any organization that aims to improve its processes and outcomes. SPC is a methodology rooted in statistical theory, which helps in monitoring and controlling processes through the use of data analytics. The significance of SPC lies in its capacity to enhance product quality and operational efficiency. Understanding the principles of SPC equips businesses with the skills to identify areas of variation within their processes, leading to informed decision-making and continuous improvement.
Definition of SPC
Statistical Process Control, often abbreviated as SPC, refers to a set of statistical techniques used to measure and analyze variations in processes. The primary aim is to determine whether a process is stable and in control or if there are factors causing unacceptable variability. By applying SPC, organizations can distinguish between common cause variation, which is inherent in the process, and special cause variation, which arises from external influences. This capability is essential as it not only improves process understanding but also fosters proactive problem-solving.
History and Evolution of SPC
The concept of Statistical Process Control emerged in the early 20th century, largely credited to Walter A. Shewhart, who introduced the control chart in 1924. This was a revolutionary advancement as it combined statistical methods with production processes. Over the decades, SPC has evolved significantly. In the 1950s, the methods were popularized in Japan by W. Edwards Deming, leading to a transformation in Japanese manufacturing practices post-World War II. Today, SPC has moved beyond manufacturing into various sectors such as healthcare, finance, and service industries. It is now recognized as a valuable quality improvement tool.
Core Principles of SPC
The effectiveness of SPC is grounded in several core principles:
- Variation: Understanding that variation is natural in processes, yet managing it is key to quality improvement.
- Control Charts: Utilizing these charts to visualize data over time, helping identify trends and deviations.
- Data-Driven Decisions: Emphasizing decisions based on statistical analysis rather than assumptions or conjecture.
- Continuous Improvement: Fostering a culture where ongoing enhancements are pursued systematically, often guided by tools like the Plan-Do-Check-Act (PDCA) cycle.
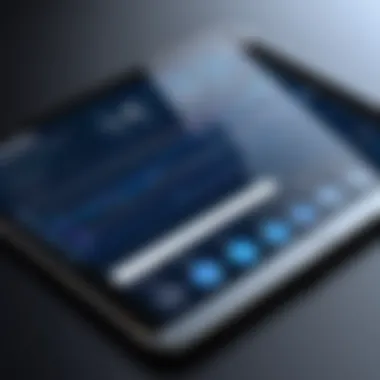

In essence, these principles ensure that organizations can effectively use SPC to optimize processes and reduce waste, driving overall performance while maintaining high standards of quality.
Key SPC Tools and Their Functions
Statistical Process Control (SPC) is crucial for businesses aiming to optimize their operational workflows. The tools used within SPC play a fundamental role in analyzing and improving processes. Each tool has specific functions that address different aspects of quality control, making them vital in a comprehensive SPC strategy. This section outlines the key SPC tools and elaborates on their functions and relevance in business operations.
Control Charts
Control charts are graphical representations used to monitor and control process variability over time. They display data points in time order, allowing teams to identify any trends or patterns that signal issues in the process. The importance of control charts lies in their ability to establish controls that prevent problems before they escalate. They help determine if a process is stable or if corrective actions are necessary.
Key benefits of control charts include:
- Visual Clarity: They provide a clear view of process behavior.
- Early Detection: They indicate variations that may require investigative actions.
- Data Driven Decisions: They guide operational decisions based on factual data rather than intuition.
Utilizing control charts effectively can lead to significant improvements in quality management. For professionals in industries like manufacturing and service, mastering this tool is essential.
Process Capability Analysis
Process Capability Analysis assesses how well a process performs concerning its specifications. This analysis produces metrics such as Cp, Cpk, Pp, and Ppk. Understanding these metrics helps businesses ascertain if their processes meet customer requirements consistently.
This tool is essential for several reasons:
- Benchmarking Quality: It establishes a baseline for quality performance.
- Informed Improvements: It provides insights into where processes may fall short.
- Enhanced Customer Satisfaction: By ensuring processes meet specifications, organizations can improve customer trust.
In today's competitive environment, companies that effectively utilize process capability analysis can gain a significant advantage over their competitors.
Pareto Analysis
Pareto Analysis, based on the 80/20 rule, assists businesses in identifying the most impactful factors contributing to issues. By focusing on the few vital causes rather than the many trivial ones, organizations can optimize their efforts to improve quality.
Performing Pareto Analysis involves:
- Collecting data on issues and their frequency.
- Creating a bar chart to visualize the most common issues.
- Prioritizing actions based on which factors present the biggest opportunities for improvement.
This method not only simplifies complex problems but also encourages teams to concentrate their resources on high-impact areas. Its effectiveness in strategic decision-making is well recognized.
Histograms
Histograms provide a visual representation of the distribution of numerical data. They depict the frequency of data points falling within defined intervals, offering insights into variability and data trends. For businesses, histograms can reveal patterns that might otherwise go unnoticed.
Their significance includes:
- Understanding Distribution: They show how data is spread across different values.
- Identifying Skewness: They can highlight anomalies or outliers that may affect performance.
- Supporting Data Analysis: They facilitate a clearer understanding of process performance.
In industries where large data sets are the norm, histograms are particularly useful for analyzing complex data sets quickly.
These SPC tools—control charts, process capability analysis, Pareto analysis, and histograms—are integral to effective quality management in business operations. The appropriate application of these tools can lead to significant improvements in efficiency, decision-making, and overall process quality, enabling organizations to thrive in a competitive landscape.
The Importance of SPC Tools in Quality Management
Statistical Process Control (SPC) tools play a critical role in the field of quality management. Their function lies in systematically monitoring and controlling processes, which allows organizations to maintain quality standards consistently. The importance of these tools extends well beyond mere compliance with regulations; they actively foster a culture of quality and continuous improvement in the workplace. Understanding how SPC tools impact quality management can lead to significant operational advantages for businesses.
Enhancing Process Efficiency
One significant benefit of SPC tools is their ability to enhance process efficiency. By monitoring key performance indicators in real-time, these tools allow organizations to identify inefficiencies quickly. For example, a control chart can highlight trends and variations in a process, enabling teams to pinpoint areas needing improvement. This immediate feedback loop facilitates timely corrective actions, which is essential for optimizing operations.
Moreover, organizations may implement tools such as Pareto analysis to focus their efforts on the most impactful issues. This prioritization ensures that resources are allocated effectively towards areas that yield the highest return on improvement efforts. As a result, efficiency increases, leading to reduced cycle times and costs.
Reducing Variability
Another area where SPC tools show their importance is in reducing variability. Variability in processes can lead to inconsistent quality, which is detrimental to customer satisfaction and can incur additional costs. SPC tools provide methodologies for quantifying this variability, enabling businesses to understand their process capabilities better.
Utilizing process capability analysis helps organizations assess how well their processes meet specifications. By identifying the sources of variability, teams can implement changes that standardize operations. This ultimately leads to predictable outcomes and consistent product quality. Furthermore, through variance reduction techniques, businesses can enhance their operational stability, boosting confidence among stakeholders.
Facilitating Decision-Making
The role of SPC tools in facilitating better decision-making cannot be overstated. With access to accurate data and analytics, decision-makers can make informed choices that align with organizational goals. SPC tools provide a structured framework for analyzing performance metrics, helping teams understand the implications of their decisions based on empirical evidence.
Furthermore, the transparency of data collected via SPC tools nurtures a data-driven culture within organizations. Leaders can confidently communicate findings to stakeholders, ensuring that everyone is aligned with strategic initiatives. The integration of data analytics in decision-making processes not only improves outcomes but also drives innovation within business operations.
"Statistical Process Control is not just a tool; it is a mindset that drives quality improvement."
Overall, the significance of SPC tools in quality management manifests through enhanced efficiency, reduced variability, and improved decision-making capabilities. By leveraging these tools effectively, organizations can achieve superior quality standards and foster a culture of continuous improvement.
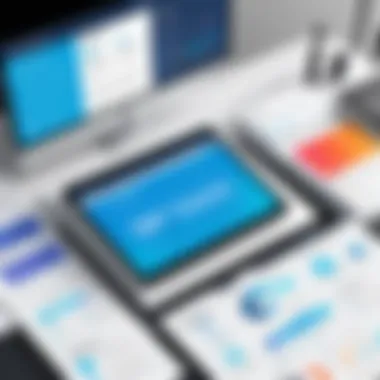

Implementing SPC Tools in Business Processes
Implementing Statistical Process Control (SPC) tools in business processes is crucial for organizations seeking to enhance their operational efficiency and maintain high-quality standards. SPC provides a structured methodology to monitor and control processes, which is essential for achieving consistent output. This section emphasizes the strategic considerations an organization must address to effectively incorporate SPC tools into their existing workflows.
Identifying Key Processes
Before deploying SPC tools, businesses must first identify the processes that significantly impact quality and performance. Not all processes may require SPC; therefore, it is vital to focus on those crucial to the organization’s goals.
To identify these key processes, consider the following:
- High variance processes: Processes with significant fluctuations in performance metrics can benefit greatly from SPC.
- Critical to quality (CTQ) areas: Processes directly affecting product or service quality should be prioritized.
- Customer complaints: Areas frequently receiving negative feedback may indicate a need for better monitoring.
Once identified, these processes can be subjected to SPC tools, which will assist in tracking their performance and detecting potential issues early.
Training Teams for Effective Use
Training is another pivotal element in implementing SPC tools. Merely having tools is not sufficient; teams must understand how to use them effectively. A thorough training program should cover the following:
- SPC Concepts: Team members need a clear understanding of SPC principles and how they apply to their specific roles.
- Tool Operation: Practical sessions on how to operate control charts, process capability analyses, and other SPC tools ensure teams can use them independently.
- Data Interpretation: Educating teams on interpreting data correctly is essential, as misinterpretation can lead to misguided decisions.
By investing in team training, businesses can significantly enhance the effectiveness of SPC implementation and foster a culture of continuous improvement.
Setting Up Control Charts
Control charts are fundamental to SPC as they visually represent process data over time and help identify trends, shifts, or potential out-of-control situations. Setting them up involves several critical steps:
- Select the relevant data: Identify which process metrics are critical for monitoring.
- Determine chart type: Choose an appropriate control chart based on the data type. For instance, use X-bar charts for means of variable data or p-charts for attribute data.
- Collect baseline data: Gather data to establish a baseline before creating control limits.
- Calculate control limits: Determine upper and lower control limits based on historical data. These limits will help identify when a process is deviating from its expected performance.
- Regularly update the charts: Control charts need to be maintained with current data to remain relevant and useful for ongoing monitoring.
Setting up control charts correctly allows data to guide decisions, enabling proactive adjustments and improvements in business operations.
By understanding and implementing SPC tools, organizations can make informed decisions, reduce variability, and enhance overall performance.
Challenges in Using SPC Tools
Despite the evident benefits of Statistical Process Control (SPC) tools, organizations often face significant hurdles in their implementation and usage. Understanding these challenges is crucial for businesses aiming to leverage SPC for improved process management and quality control. Addressing these obstacles not only optimizes the utility of SPC tools but also enhances overall operational efficacy.
Data Collection Issues
A primary challenge in effective SPC tool usage is data collection. Accurate data is the foundation of any SPC application. If the data collected is flawed, the insights derived from SPC will also be unreliable. Many organizations struggle with gathering consistent and high-quality data. Factors contributing to data collection issues may include:
- Inadequate Systems: Existing data management systems may not be sufficient, lacking the capacity to collect real-time data accurately.
- Human Error: Manual data entry is prone to mistakes, leading to inconsistencies that can skew process analysis.
- Lack of Standardization: Without standardized data collection methods, variations may occur across different teams or departments, making it hard to obtain a clear picture of business processes.
Investing in an appropriate data management system and training staff on data entry best practices can substantially ameliorate these issues.
Resistance to Change
The integration of SPC tools often meets with resistance to change from employees. People are generally accustomed to established workflows, and altering those can be confrontational. Key factors behind this resistance include:
- Fear of the Unknown: Employees might be wary of how new tools will disrupt existing processes and routines.
- Perceived Complexity: If workers view SPC tools as overly complex, they may hesitate to embrace them fully or utilize them correctly.
- Cultural Barriers: In some organizations, a lack of a quality-driven culture can inhibit acceptance of new practices.
To reduce resistance, organizations should engage employees early in the process, providing comprehensive training and emphasizing the benefits SPC tools will bring to their work.
Misinterpretation of Data
Interpreting the data generated by SPC tools can be problematic. Misinterpretation of data can lead to misguided strategies and potentially harmful decisions. Common pitfalls include:
- Lack of Training: Employees may not have the necessary statistical background to analyze the data in a meaningful way.
- Overemphasis on Outliers: Focusing too heavily on outlier data points can distort the understanding of overall process performance.
- Ignoring Context: Misreading results without considering contextual information may lead to incorrect conclusions.
To counteract these issues, organizations need to offer robust training on data analysis as part of the SPC implementation process. Furthermore, encouraging collaboration among employees can help ensure various perspectives are considered when interpreting data.
The successful implementation of SPC tools hinges on overcoming resistance to change, ensuring accurate data collection, and facilitating proper data interpretation.
By recognizing and addressing these challenges, businesses can maximize the advantages of SPC tools, driving forward quality management and process improvement.
Case Studies: SPC Tools in Action
The exploration of Statistical Process Control (SPC) tools through real-world case studies offers compelling evidence of their applicability and effectiveness in various industries. These case studies serve as practical illustrations, demonstrating not only how SPC tools can be integrated into daily operations but also the tangible benefits derived from their implementation. They highlight key elements such as the unique challenges faced by different sectors, innovative solutions adopted, and measurable improvements in quality and efficiency. This section emphasizes that effective utilization of SPC tools can lead to enhanced process reliability, increased customer satisfaction, and significant financial returns.
Manufacturing Sector Example
In the manufacturing industry, SPC tools have become integral to maintaining product quality and optimizing production processes. One notable example involves a large automotive manufacturer that implemented control charts to monitor assembly line operations. By continuously analyzing data from various stages of production, the company was able to identify consistency issues in part dimensions. As a result, the manufacturer diagnosed a recurring machining defect stemming from equipment wear.
The following benefits were observed as a direct consequence of using SPC tools in this case:
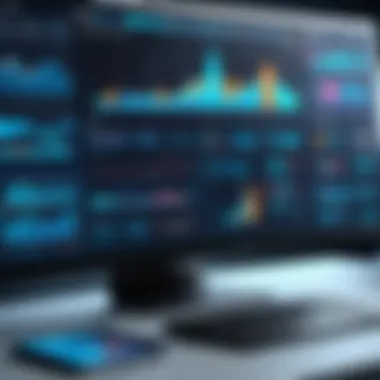

- Reduced Defect Rates: The implementation of control charts led to immediate detection of deviations, allowing for rapid corrective actions.
- Cost Savings: Through improved quality, the company significantly decreased waste and rework costs, amounting to millions of dollars annually.
- Enhanced Employee Training: Workers became more familiar with data analysis, thus promoting a culture of quality and accountability on the shop floor.
SPC tools not only provided immediate insights into the production process but also fostered a long-term commitment to continuous improvement.
Service Industry Implementation
The service industry also benefits from SPC tools, as demonstrated in a case study of a healthcare organization aimed at improving patient care and operational efficiency. This organization deployed process capability analysis alongside Pareto analysis to address long waiting times in its outpatient clinics. By gathering data on patient flow, staff workloads, and service times, the clinic identified key bottlenecks in the scheduling system.
Key outcomes from the implementation included:
- Improved Patient Experience: With reduced waiting time, patient satisfaction scores increased significantly, demonstrating the impact of SPC tools on service quality.
- Optimized Resource Allocation: The clinic adjusted staff schedules based on peak patient arrival times, utilizing data-driven insights to improve workforce efficiency.
- Sustainable Practices: Continuous monitoring of metrics established a framework for long-term performance improvements and priority setting.
These examples underline the versatility of SPC tools across varied contexts, confirming their importance in addressing industry-specific challenges while yielding significant returns on investment.
Evaluating the ROI of SPC Tools
In any business decision, understanding the return on investment (ROI) is crucial. Evaluating the ROI of SPC tools is no exception. These tools aim to enhance quality and efficiency in operations, but quantifying their impact is essential to justify their adoption. Investing in SPC tools can often require considerable financial resources. Therefore, a systematic evaluation is vital for decision-makers.
One major element to consider in ROI evaluation is the potential for cost savings. By reducing defects and improving process efficiency, businesses can lower operational costs significantly. When SPC tools are implemented, companies often experience fewer errors, which directly translates to decreased waste and rework costs. This not only increases profit margins but also enhances customer satisfaction by delivering higher-quality products or services.
Another critical consideration is the time saved through automation and improved processes. SPC tools can provide timely insights into process performance, allowing teams to respond more swiftly to any deviations from the norm. This agility in operations means that companies can better utilize their resources, leading to more efficient workflows and ultimately better financial outcomes.
Additionally, improved data visibility and analysis through SPC tools can facilitate strategic planning. A robust understanding of data trends from control charts or Pareto analysis allows organizations to make informed future investments and operational decisions, further enhancing ROI.
"Evaluating ROI is not just about the numbers; it’s about understanding the long-term benefits of investing in quality management tools."
Cost-Benefit Analysis
A cost-benefit analysis (CBA) provides a structured way to evaluate the financial implications of adopting SPC tools. This involves detailing all costs associated with the implementation, including software expenses, training, and ongoing maintenance.
- Direct Costs: These include expenses for the SPC software itself, as well as training for employees. Companies need to factor in the time employees spend learning the tools, which is a cost in itself.
- Indirect Costs: These might be harder to quantify but include things like disruption to existing workflows during the transition phase.
- Long-Term Savings: Anticipated savings from reduced waste, fewer errors, and enhanced operational efficiency should be factored as well.
Once the costs are identified, the potential benefits should be estimated. Benefits may include:
- Reduced waste production.
- Increased customer satisfaction.
- Higher productivity levels.
- Enhanced team morale through improved processes.
After all costs and benefits are identified, calculating the overall ROI can provide a clear picture of the financial advantage of implementing SPC tools. A positive ROI indicates a worthwhile investment, reinforcing the decision to proceed.
Performance Measurement Metrics
Measuring performance effectively is fundamental to evaluating the ROI of SPC tools. Metrics can provide insights into how well tools are performing and their actual impact on the operation. Common performance measurement metrics include:
- Defect Rate: This metric quantifies the number of defects per unit produced. A decrease in this metric suggests improved quality due to effective SPC tools.
- Cycle Time: This indicates the total time from the beginning to the end of a process. A shorter cycle time signifies better operational efficiency.
- Process Capability Index (Cpk): This identifies how consistently a process operates within specified limits. A higher Cpk value reflects a more capable process.
- Return on Quality (ROQ): This metric assesses the monetary return gained from quality initiatives versus investments made in quality improvement.
Using these metrics, organizations can track the effectiveness of their SPC tools over time. Regular evaluations against these performance metrics not only validate the decisions made but also pinpoint areas for further improvement, fostering a culture of continuous enhancement.
Future Trends in SPC Tools
As the landscape of business operations evolves, the significance of Future Trends in SPC Tools becomes increasingly paramount. These trends not only shape how organizations engage with Statistical Process Control but also alter the very fabric of decision-making and operational efficiency. Understanding these trends allows businesses to leverage new technologies, ensuring they remain competitive and effective.
Integration with AI and Machine Learning
The integration of Artificial Intelligence and Machine Learning with SPC tools represents a significant turning point for businesses. By automating data analysis, companies can uncover insights that are beyond human capabilities. SPC tools empowered with AI can identify patterns in data that indicate potential issues before they manifest into serious problems. For instance, machine learning algorithms can be trained on historical process data to predict future process behavior, drastically improving response times.
Moreover, predictive analytics can enhance decision-making frameworks. This means less time spent on data sorting and more focus on strategic initiatives. SPC tools that integrate AI can also facilitate proactive monitoring of key performance metrics, allowing teams to implement corrective measures faster.
"Utilizing AI in SPC is not just about efficiency; it's about transforming how we perceive and react to data in real time."
Advancements in Data Analytics
The realm of data analytics is transforming rapidly, and its advancements directly impact SPC tools. Enhanced data analytics allows for the processing of more complex datasets with greater accuracy. Tools that incorporate advanced analytics features, such as real-time data visualization and interactive dashboards, enhance the understanding of variations and trends within business processes.
Furthermore, with the advent of Big Data technologies, organizations can analyze vast quantities of data swiftly. Real-time analytics enable timely decisions, which are crucial for staying ahead in competitive markets. Companies can use analytics to drill down into specifics, identify root causes of process deviations, and develop targeted improvement plans.
In summary, embracing future trends in SPC tools effectively positions businesses to navigate complexities in operations. Organizations that integrate AI and leverage advancements in data analytics are not just adapting; they are setting the stage for innovation and excellence in their processes.
Finale
In this concluding section, we synthesize the significance of Statistical Process Control (SPC) tools in business operations, emphasizing their role in enhancing quality management. The adoption of SPC tools fosters a culture of continuous improvement and accountability within organizations.
SPC tools, such as control charts and process capability analysis, provide valuable insights into production processes. These tools not only highlight areas of variability but also enhance decision-making capabilities. By utilizing data effectively, businesses can identify trends and respond swiftly to anomalies. This capacity to respond is essential in today’s competitive landscape, where organizations must strive to preempt issues before they escalate.
Moreover, using SPC tools can lead to cost reductions by minimizing defects and waste. Businesses can realize substantial savings through improved efficiency and reduced rework. The performance measurement metrics gained through SPC also allow for standardized evaluations across various departments. This consistency ensures that all processes align with broader organizational goals.
It's important to consider the challenges of implementing SPC tools, such as data collection issues and potential resistance from teams. However, addressed appropriately, these challenges can be mitigated. As organizations increasingly adopt technology, integrating SPC tools with modern data analytics and machine learning can enhance their effectiveness and usability.
"The future of SPC in business operations lies in its integration with emerging technologies, making it more adaptable and powerful for quality management."
SPC tools are essential for organizations that prioritize quality and efficiency. As businesses navigate the complexities of production and services, the insights derived from SPC will become even more critical. Thus, decision-makers should consider implementing these tools not just as options but as pivotal components in their operational strategies.