Mastering Inventory Management with the ABC System
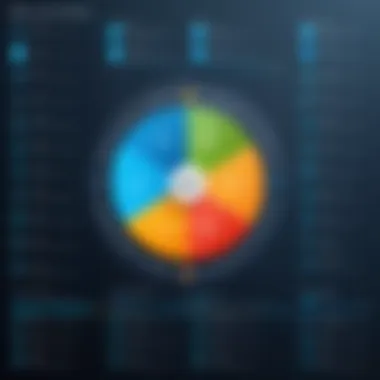
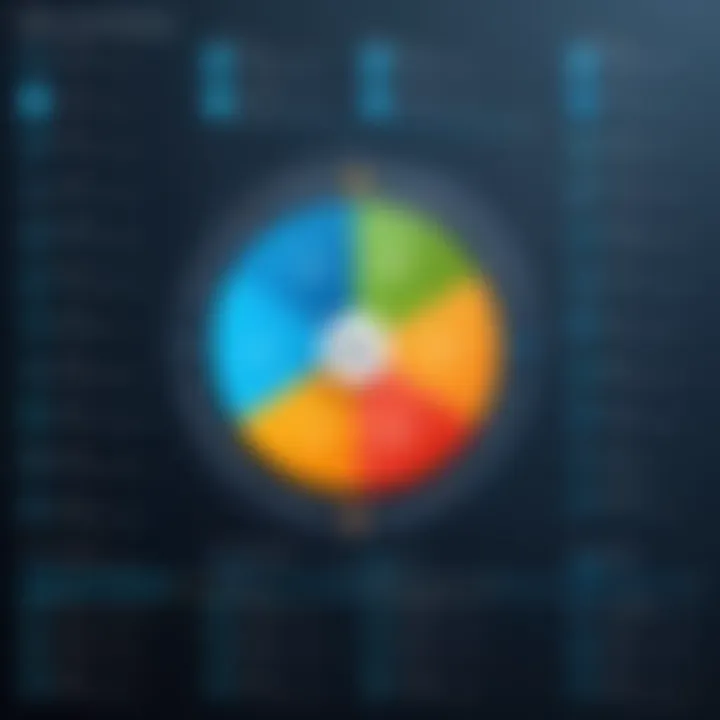
Intro
Inventory management is a vital component of any business operation. One method that has gained prominence for enhancing inventory efficiency is the ABC System Inventory. This classification method prioritizes inventory items based on their importance to the business, enabling better control and management.
The ABC classification divides inventory into three categories: A, B, and C. 'A' items are high-value items with low frequency of sales, 'B' items are moderate in both value and sales frequency, while 'C' items are low in value but may have a high turnover rate. This classification helps organizations focus their resources more effectively.
Understanding the ABC System can significantly optimize inventory processes, ensure that capital is not tied up in unnecessary stock, and streamline operations. This article will provide a comprehensive exploration of the principles behind the ABC classification, its implementation strategies, key benefits, and its necessity in todayβs business environment.
Software Overview
To optimize inventory management further, various software solutions exist that facilitate the ABC classification process. These tools help organizations categorize items effectively and manage stock levels based on the insights derived from ABC analysis.
Software Description
The software typically includes functionalities that allow users to classify items into the ABC categories, track inventory levels, and forecast future inventory needs. Features may range from basic classification to advanced reporting and analytics tools to aid decision-making.
Key Features
- Classification Tools: Simplify the sorting of inventory items into A, B, and C categories.
- Real-Time Tracking: Monitor stock levels dynamically to avoid stockouts or excess inventory.
- Reporting Analytics: Generate reports that visualize inventory performance across categories.
- Integration Capabilities: Seamlessly connect with other software used in supply chain management or ERP systems.
Pricing Models
Organizations can choose from various pricing models when selecting inventory management software. Understanding these can help in making informed budgeting decisions.
Subscription Options
Many software providers offer a subscription-based model, which often includes:
- Monthly or Annual Payments: Users pay a recurring fee to access the service.
- Tiered Pricing: Different features are available at various pricing levels, allowing for scalability based on business needs.
One-Time Purchase
Some vendors also offer a one-time purchase option, generally accompanied by:
- Lifetime Access: A single payment grants ongoing access to the software without recurring fees.
- Limited Updates: Future updates may require additional purchases or fees, depending on the vendor's policy.
Understanding the pricing structure is essential for organizations to effectively budget for their inventory management solutions.
"Utilizing a systematic approach to inventory classification can lead to significant operational efficiency improvements throughout the entire supply chain."
The following sections will delve deeper into the implementation of the ABC System and the manifold benefits it offers, helping decision-makers fully grasp its relevance in today's business landscape.
Defining the ABC System Inventory
Defining the ABC System Inventory is crucial as it lays the foundation for an efficient inventory management strategy. The ABC classification helps in understanding which items are most critical in the inventory and how resources should be allocated accordingly. Organizations can leverage this method to improve their inventory control, leading to enhanced productivity. Focusing on the essential elements, the ABC system identifies high-impact items and ensures that they are managed effectively. This tailored approach allows businesses to enhance decision-making and optimize inventory turnover rates.
Overview of Inventory Management
Inventory management encompasses the processes involved in ordering, storing, and utilizing a company's inventory. Effective inventory management is vital because it influences cash flow, production, and customer satisfaction. Organizations need to maintain the right level of stock to meet demand without overstocking items that may become obsolete or underutilized. By employing an organized system, companies can ensure timely procurement and distribution of products.
In today's fast-paced market, the need for efficient inventory management is greater than ever. Companies face challenges like fluctuating demand and supply chain disruptions. Therefore, understanding the principles of inventory management remains essential. It does not only optimize operations but also drives profitability.
What is ABC Classification?
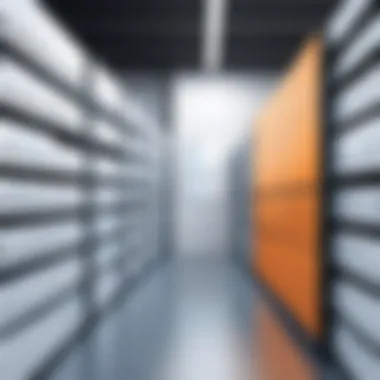
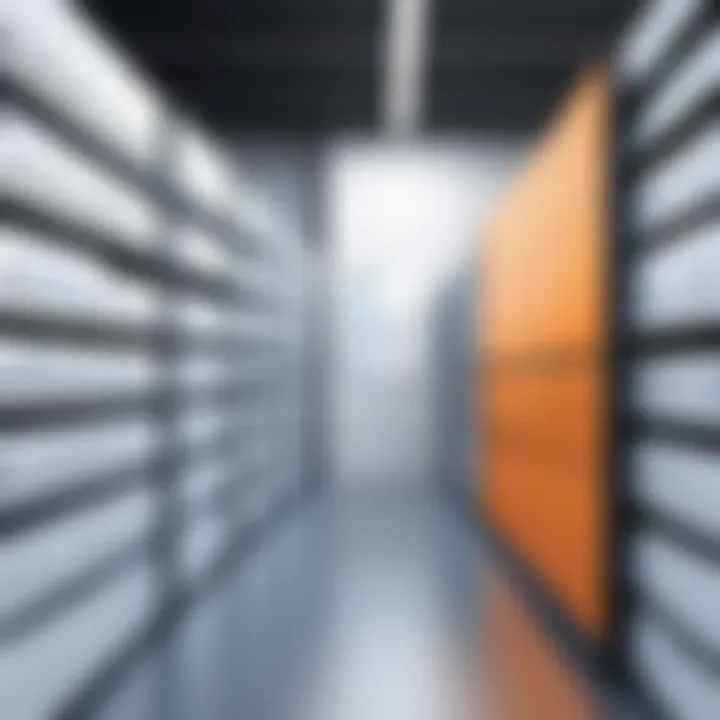
ABC Classification is a categorization method that organizes inventory into three distinct categories based on various criteria, primarily value and turnover rate. This system ranks items based on their importance to the business.
- A items are high-value products that typically comprise a small percentage of total items but represent a large portion of overall inventory value. They require tight control and frequent review.
- B items are of moderate value and are often monitored less stringently than A items. Their management typically falls somewhere between A and C items.
- C items encompass low-value goods that can be ordered or stocked with less frequency and detail. They require minimal management attention.
By categorizing inventory items in this way, organizations can allocate resources where they matter most and streamline their operations.
The primary goal of ABC Classification is to ensure that business resources are focused on the items that will contribute the most to overall profitability while managing the less critical inventory more efficiently. This method highlights the importance of prioritization in inventory management and leads to significant improvements in efficiency and effectiveness.
Principles Underpinning the ABC System
The ABC system is grounded in specific principles that enhance inventory management. These principles facilitate better decision-making for businesses and organizations. Adopting the ABC method leads to more efficient inventory control, allowing for better allocation of resources. By understanding the principles behind this system, stakeholders can employ strategies that directly contribute to enhancing operational efficiency. The focus on categorization forms the core of this methodology, influencing how inventory is evaluated and managed.
The Pareto Principle in Inventory
The Pareto Principle, often referred to as the 80/20 rule, asserts that a small portion of inventory items typically accounts for a majority of inventory value. In the context of the ABC system, this principle underlines the necessity to identify high-impact inventory items. This identification allows businesses to focus their resources on managing these crucial items effectively. The significance of this principle lies in its ability to inform strategy and facilitate prioritization in inventory management.
Categorization of Inventory Items
Categorization within the ABC system segments inventory into three distinct classes: High-Value, Moderate-Value, and Low-Value Items. This categorization aids in tailoring inventory management approaches to specific item classes, thus optimizing control and minimizing costs.
High-Value Items
High-Value Items represent a small segment of the overall inventory but contribute significantly to the total value. Their key characteristic is their high cost or revenue generation potential. These items typically warrant increased attention due to their financial impact. For instance, items like machinery or specialized components may fall under this category. By prioritizing these items, businesses can streamline processes, reduce the risk of stockouts, and ensure that critical assets remain in optimal supply. However, focusing too narrowly on high-value items can lead to neglect of lower-value items that still need attention.
Moderate-Value Items
Moderate-Value Items hold a transitional position in the inventory spectrum. They represent a larger quantity than high-value items but contribute less to overall inventory value. The key characteristic of these items is their balance between cost and frequency of use. Effective management of these items helps in maintaining a streamlined operation without overspending or overstocking. Their unique feature is the potential for moderate risk when poorly managed. By considering their needs, businesses can avoid unnecessary complications in inventory control.
Low-Value Items
Low-Value Items represent the bulk of inventory in many organizations. Despite their low individual value, they can still pose challenges in terms of management. Their key characteristic is their high volume and low cost, making them more of a logistical concern than a financial one. A potential downside of focusing less on these items is the risk of operational inefficiencies that arise from stockouts or wastage. Nonetheless, managing low-value items efficiently can lead to reduced overhead costs and improved inventory turnover.
Implementing the ABC System
The implementation of the ABC System is a crucial aspect of any inventory management strategy. A well-planned approach not only enhances operational efficiency but also allows organizations to focus their resources on the most critical inventory items. This section delves into practical steps to integrate the ABC classification into existing inventory practices.
Efficient implementation can lead to substantial improvements. It helps in identifying high-value items that require more attention, thus reducing losses and improving service levels. It also allows businesses to allocate resources wisely, resulting in better inventory turnover and customer satisfaction.
Steps for Implementation
Implementing the ABC System involves several key steps:
- Analyze Current Inventory: Begin by reviewing your existing inventory. This involves gathering data on all items, including costs, usage rates, and turnover frequencies. This analysis will provide a baseline for classifying items.
- Establish Classification Criteria: Determine the criteria that will be used for classification. Commonly, the criteria involve both monetary value and usage frequency. High-value items might be 80% of inventory costs but only include 20% of the items.
- Classify Inventory Items: Based on your criteria, categorize items into three classes: A, B, and C. High-value items, which are critical to financial performance, should be classified as 'A.' Moderate and low-value items will fall into categories 'B' and 'C' respectively.
- Apply Management Strategies: Develop specific management strategies for each category. For instance, 'A' items may need tighter controls and more frequent reviews, while 'C' items could be managed with more relaxed oversight.
- Monitor and Adjust: Once implemented, continuously monitor the inventory system. Evaluate whether classifications need to change based on shifting business dynamics, customer demands, or market conditions. Adjustments ensure that the system remains effective over time.
Following these steps will lay a solid foundation for a successful ABC inventory management system.
Technological Support for Implementation
Modern technologies play a pivotal role in the implementation of the ABC System. Various software solutions can streamline processes, making inventory management far more efficient.
- Inventory Management Software: Tools like SAP Business One and NetSuite provide integrated solutions that help categorize items based on their ABC classification. These platforms offer insights into item performance, enabling data-driven decisions.
- Data Analytics Tools: Leveraging data analytics helps in better understanding usage patterns and trends. Tools such as Tableau and Power BI can visualize inventory data, allowing organizations to see which items require more focus.
- Automation: Automation technologies can support inventory monitoring, making real-time adjustments without manual intervention. Systems can alert managers when 'A' items are running low, thus maintaining optimal stock levels.
- Cloud-based Solutions: Implementing cloud-based systems enhances accessibility and collaboration. Teams can access inventory data remotely, ensuring that every stakeholder has the right information.
Technological support not only simplifies the implementation but also fosters continuous improvement in inventory management practices. Organizations that embrace these tools will likely see improved accuracy and efficiency in their ABC classification efforts.
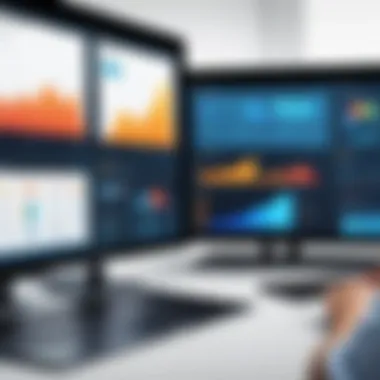
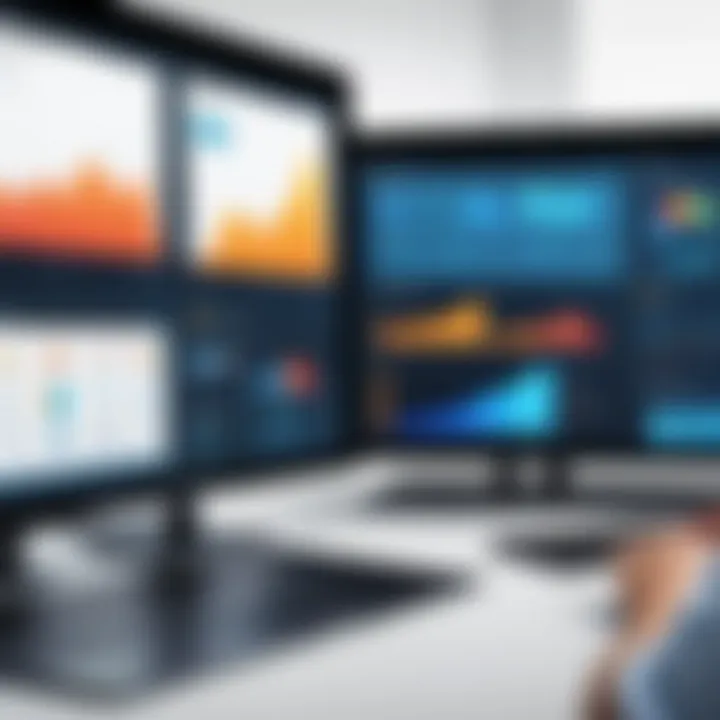
Benefits of the ABC System Inventory
The ABC System Inventory is crucial for modern inventory management. Organizations are continuously seeking ways to optimize operations and resources. The ABC model not only provides a structured methodology for categorizing inventory but also enhances operational efficiency, enabling firms to respond promptly to market demands. This section will elaborate on two primary benefits of the ABC System Inventory: enhanced inventory control and improved resource allocation.
Enhanced Inventory Control
Effective inventory control is the bedrock of any successful organization. The ABC System helps businesses maintain a tight grip on their resources by categorizing items based on their importance and value. High-value items, or A items, warrant strict control due to their significant effect on the bottom line. Monitoring these items closely minimizes the risk of stockouts or excess inventory, which can cripple an operation.
Understanding stock levels play a critical role in this. With the ABC System, organizations can prioritize management efforts on A items while applying more lenient controls on C items, which are of lower value. This targeted approach allows teams to focus on critical inventory facets, making it easier to align supply with demand.
Additionally, implementing the ABC System can facilitate better forecasting. By recognizing patterns in inventory consumption, organizations can leverage historical data for future planning. This leads to more accurate stock levels, reducing costs associated with over or under stocking. As a result, overall inventory accuracy is increased, leading to smoother operations and satisfied customers.
"The ABC System transforms chaos into order, allowing businesses to find clarity in their inventory decisions."
Improved Resource Allocation
In a competitive market, resource allocation is an essential element for sustained success. The ABC System aids organizations in directing their attention and resources to areas that yield the highest return on investment. By categorizing inventory into A, B, and C items, businesses can establish clear priorities.
For example, financial resources can be allocated more efficiently, investing the bulk in A items that directly impact profitability. In contrast, resources tied to low-value C items can be minimized, thus freeing up capital for more impactful areas. This strategic allocation not only maximizes returns but also enhances the firm's agility in responding to market changes.
Moreover, workforce productivity is enhanced through optimized resource allocation. Employees can focus on managing critical items rather than spreading themselves too thin across a vast range of items with low importance. This leads to a more engaged workforce and better results overall.
In summary, the ABC System Inventory provides organizations with substantial benefits through enhanced inventory control and improved resource allocation. These advantages ultimately contribute to operational excellence, enabling companies to thrive in a dynamic business environment.
Challenges in the ABC System Implementation
Implementing the ABC System Inventory poses specific challenges that organizations must navigate to ensure its success. Understanding these challenges is crucial because they can determine the level of effectiveness of the system. Addressing these challenges effectively can enhance overall inventory management, streamline operations, and ultimately contribute to better resource utilization. Below are some prominent concerns that warrant consideration.
Resistance to Change
One of the fundamental problems encountered during the implementation phase is resistance to change. Employees may view the new system as an unwelcome alteration to their routine. Such resistance can stem from several factors, including a lack of understanding of the ABC classification's benefits, fears of job security, and discomfort with new technological tools.
To ease this transition, organizations should focus on communication. Providing clear information about why the ABC system is being adopted and how it will benefit the staff and overall performance is critical. Training sessions and workshops can play an important role in familiarizing employees with the new protocols and mechanics of the ABC system. Additionally, involving employees in the planning and implementation process can help reduce resistance and foster a sense of ownership.
Data Accuracy Concerns
Another significant challenge pertains to data accuracy. The effectiveness of the ABC system relies heavily on the precision and reliability of inventory data. Inaccurate data can lead to misclassification of items. As a result, these errors can distort the categorization of inventory and impair decision-making processes. Organizations often struggle with outdated data, manual entry errors, and inconsistent data management practices, which exacerbate these issues.
To mitigate data inaccuracy, companies should invest in robust inventory management software that integrates seamlessly with existing systems. Regular audits of inventory data can help identify discrepancies and maintain high standards of accuracy. Furthermore, creating a culture of accountability where employees are responsible for their contributions to inventory data can significantly enhance accuracy in the long term.
Effective data management is key to a successful ABC system. Inaccurate data undermines the entire classification system.
By recognizing and addressing resistance to change and data accuracy concerns, organizations can better position themselves to successfully implement the ABC system. This proactive approach not only smooths the transition but also fosters an environment where informed decision-making prevails and ultimately contributes to improved inventory management.
Case Studies on ABC System Success
Examining case studies on the ABC System can offer invaluable insights into its practical application across different industries. These narratives not only provide evidence of the system's effectiveness but also highlight specific challenges and solutions encountered by organizations. Understanding these real-world examples helps to contextualize the abstract principles discussed earlier. By observing how various sectors implement the ABC classification, decision-makers can better appreciate its nuances and adapt strategies to their own contexts.
Moreover, the success stories from these case studies serve as motivation. They demonstrate that the ABC System is not just theoretical; it has been successfully executed in varied environments. The transferable lessons from these instances can guide companies in fine-tuning their inventory management strategies.
Manufacturing Sector Examples
The manufacturing sector often deals with large volumes of diverse inventory, making it a prime candidate for the ABC System. For instance, consider a company like General Motors. They utilized the ABC classification to optimize their parts inventory. The classification allowed them to categorize parts based on value and usage frequency.
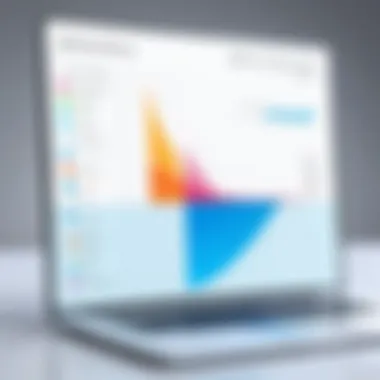
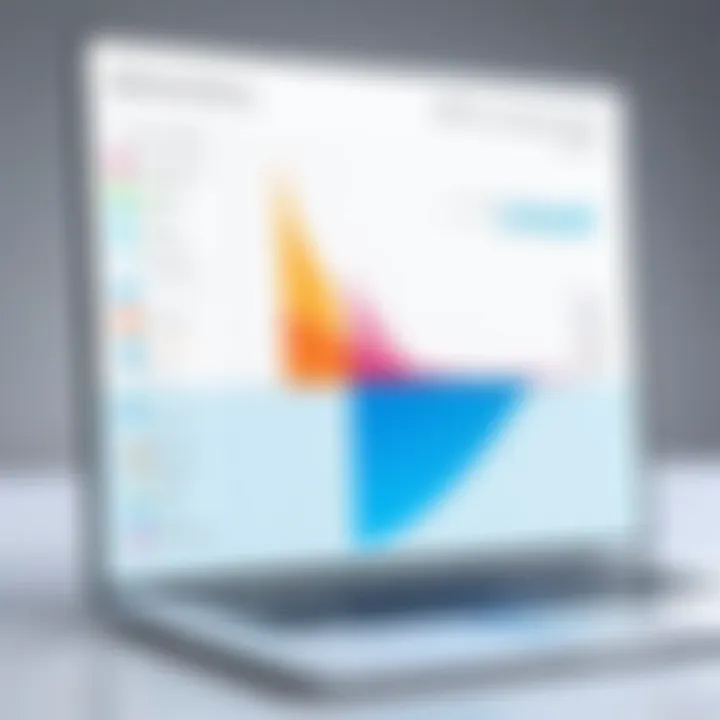
Key Benefits Noted:
- Cost Reduction: By focusing on high-value, high-usage items, the company reduced holding costs significantly.
- Efficiency in Procurement: Streamlining reorder processes ensured they did not bottleneck production with lack of critical parts.
Another example can be found in the electronics manufacturing sector, where Samsung Electronics applied the system to manage its components. This approach helped to not only balance inventory but also reduce waste, aligning stock levels with production requirements. By prioritizing inventory tailored towards best-selling products, they enhanced responsiveness to market demands while minimizing excess stock.
Retail Sector Applications
In the retail industry, the ABC System is equally transformative. A notable case study is Walmart. The retail giant implemented an ABC inventory management system to refine its stock management practices. By identifying and categorizing products, Walmart ensured that fast-selling items, like grocery necessities, were always well-stocked, while slower-moving items received manageable oversight.
Key Highlights:
- Optimized Shelf Space: The classification enabled better allocation of shelf space, enhancing customer experience.
- Sales Forecasting: Data derived from the system improved forecasting accuracy, allowing for better seasonal planning.
Another pertinent example comes from Zara, a leader in fast fashion. Zara's dynamic inventory management realigned quickly with fashion trends, which vary rapidly. By focusing on high-demand categories, the retailer reduced unsold inventory and improved turnover rates. Their responsive approach derives from the principles set out in the ABC framework, illustrating its applicability in a fast-paced retail environment.
These case studies underscore the versatility and adaptability of the ABC System across various sectors, proving its effectiveness in addressing complex inventory challenges.
Future of the ABC System Inventory
The evolution of the ABC System Inventory is becoming more relevant as businesses face rapid changes in technology and market demands. This section highlights the impact of integrating advanced technologies and the need for adaptability in inventory management strategies. Understanding the future direction of the ABC system can lead to more efficient operations and better inventory control.
Integration with AI and Machine Learning
Artificial Intelligence (AI) and Machine Learning are transforming how organizations manage their inventories. Integration of these technologies into the ABC System can yield significant benefits. For example, AI algorithms can analyze vast amounts of data to identify patterns. This capability enhances the accuracy of inventory classification, reducing manual errors. Additionally, AI can forecast demand more effectively, allowing businesses to adjust their inventory levels proactively.
Some notable advantages of integrating AI into the ABC system include:
- Increased Efficiency: Machine learning can optimize inventory levels based on real-time data. This means businesses can minimize overstock and stockouts.
- Cost Reduction: By utilizing AI for inventory management, companies can lower their operational costs, thanks to improved decision-making.
- Dynamic Classification: AI systems can adapt classifications based on changing market conditions, ensuring that the ABC system remains relevant.
"The successful implementation of AI in inventory management can serve as a game changer for many businesses, leading to a more sustainable approach in the long run."
Evolving Business Needs
As market conditions fluctuate, businesses must adapt their inventory management practices. The ABC System, while effective, should not remain static. Evolving business needs require organizations to constantly assess and refine their inventory strategies.
Considerations for adapting the ABC System include:
- Customer Expectations: The rise of e-commerce has led to higher customer expectations for speed and accuracy. Businesses must align their inventory systems to meet these demands.
- Supply Chain Disruptions: Global events can impact supply chains significantly. Organizations need agile inventory systems that can quickly respond to changes in supply and demand.
- Sustainability Goals: More companies are focusing on sustainable practices. The ABC System can facilitate better resource allocation tied to sustainable practices, including waste reduction and inventory turnover.
By addressing these evolving needs, organizations can not only survive but thrive in a competitive landscape. Adaptability in the ABC System is key to maintaining relevancy and ensuring operational effectiveness.
Closure
In any discussion surrounding inventory management, the conclusion serves as a pivotal point of reflection. It encapsulates the essential ideas and underscores the implications of implementing the ABC System Inventory. Not only does this approach contribute to inventory categorization, but it also enhances strategic decision-making. The ability to distinguish between high-value and low-value items allows organizations to allocate resources more effectively.
Summarizing Key Takeaways
The ABC System offers numerous advantages that directly influence operational efficiency. Here are the key takeaways:
- Effective Resource Allocation: Focuses on items that are vital for revenue and operational capabilities, ensuring that resources and attention are directed where they matter most.
- Streamlined Inventory Management: Simplifies the process of monitoring and managing inventory levels by emphasizing the critical nature of different items.
- Enhanced Control: Provides companies a clearer picture of their inventory dynamics, allowing for better forecasting and planning.
- Improved Operational Efficiency: By concentrating efforts on high-impact items, businesses can reduce carrying costs related to low-value items.
Looking Ahead at Innovations
As businesses evolve, the integration of advanced technologies remains crucial for the future of the ABC System Inventory. Potential innovations include:
- AI and Machine Learning: These technologies can offers predictive analytics that optimize inventory management further by forecasting demand and adjusting categorization dynamically.
- Real-Time Data Analytics: With tools like ERP systems, companies can harness real-time data to make more informed decisions about inventory.
- Automated Replenishment: The application of AI can lead to automated restocking processes, ensuring that high-value inventory is consistently available without overstocking low-value items.
As organizations anticipate new trends and develop methods to improve inventory management, the principles behind the ABC System will continue to be relevant. It is a platform that encourages businesses to adapt and thrive in a changing marketplace.